キャンプバーナーといえばSOTO
キャンプバーナーの代名詞ともいえる超定番人気バーナー、SOTOのST-310。ゴトクと脚を兼ねた機能美あふれる形状や、収納性の高さでキャンプツーリングでも定番のアイテム。
ちなみに商品名にあるレギュレーターストーブなんだけど、これはレギュレーターが安定した火力の維持や低温時の動作を飛躍的に向上させるという、SOTOならではの機構。
レギュレーターについては、また後日詳しく記事にするね。
ソト (SOTO) 日本製 シングルバーナー マイクロレギュレーター搭載(高火力・風に強い) CB缶 グループ キャンプ レギュレーターストーブ Range(レンジ) ST-340 シルバー
amzn.toそして、最新モデル。
2024年4月に登場したST-350は、まさに究極のシングルバーナー。ST-310で好評だった機能美などは継承しつつ、点火ノブの追加などの機能向上と軽さを追求した逸品。
ゴトクは3本になり、さらに材質もチタンに。その他にも徹底した軽量化により、重量わずか135g。
ソト(SOTO) 日本製 シングルバーナー マイクロレギュレーター搭載(高火力 風に強い) CB缶 軽量 コンパクト 収納ポーチ付 ハイパワー カセットボンベ ソロ デュオ キャンプ トレッキング 登山 レギュレーターストーブ TriTrail(トライトレイル)・CB TOUGH 125セット ST-350TB
amzn.toさらにハイパワーカセットボンベST-711と組み合わせることで、-5度でも使用可能という、CB缶バーナーの常識を超えた耐寒性能を実現。
ちなみに自分が愛用してるのはGストーブことST-320。レギュレーターこそ搭載してないものの、メスティンにシンデレラフィットなコンパクトさと精度の高い展開方式が最高。バイクキャンプに最適な名作バーナーだよ。
新富士バーナー(SOTO) Gストーブ ST-320(新富士 新富士バーナー SOTO 調理器具 バーナー ストーブ ピクニック 一人用 料理 調理 バイク オートバイ キャンプ)
amzn.to愛知県豊川市の新富士バーナー本社工場に行ってみる
さて、そんな魅力あふれるアイテムを愛知県豊川市で生産してるということで、連絡を取って特別に工場見学をさせていただくことにしたよ。
新富士バーナー株式会社があるのは愛知県豊川市の御津町。御津町は、みとちょうって読むよ。このあたり、難読地名多いのよね。宝飯(ほい)とか。御津はみとだけど、その近くにある御油はごゆだったり。罠。
今回は久々にスーパーカブ90で向かうよ。
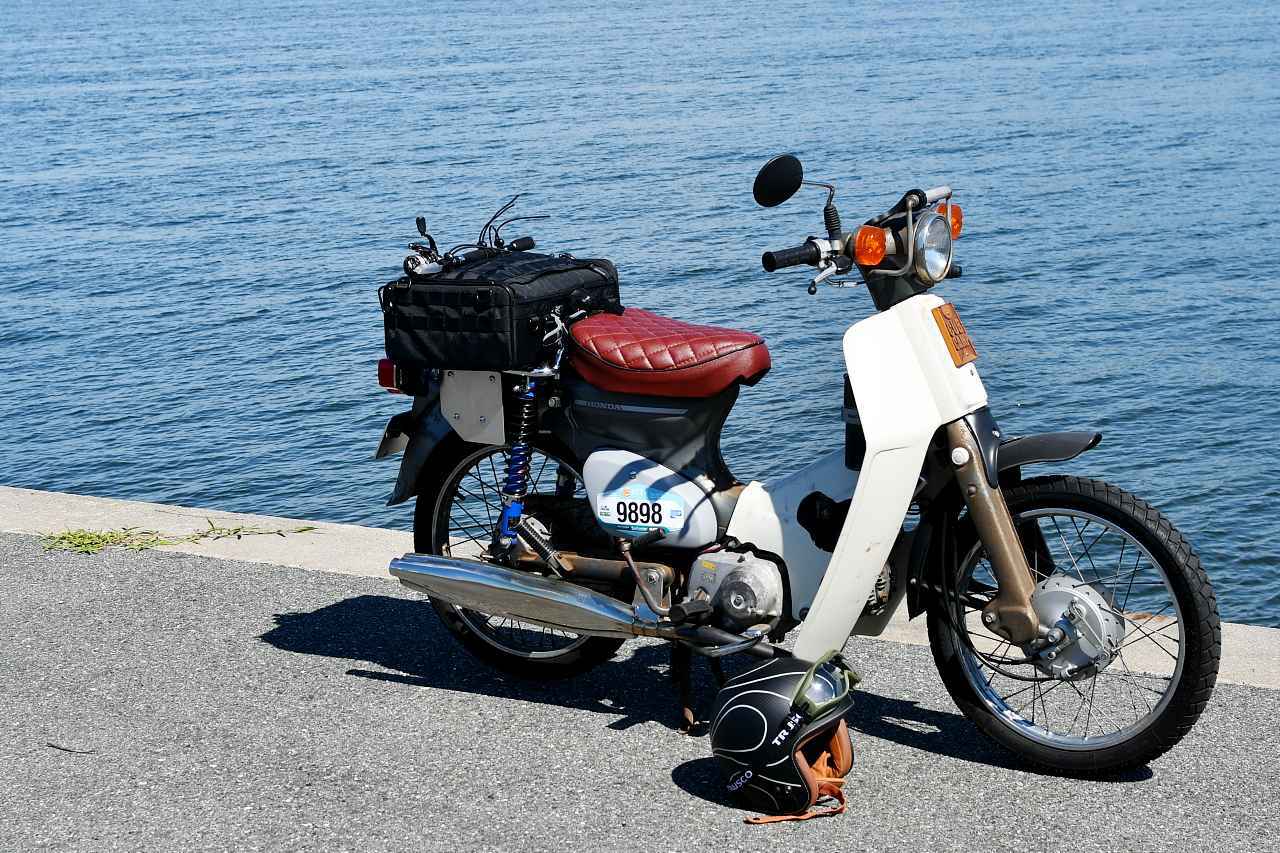
1時間以上早く着いちゃったので、近くで釣りをして時間をつぶすのだ。
対岸のさらに向こうにSOTOがあるはず。
アカエイが泳いでた。
あとチビイワシが泳いでた。ベイトがのんびりしてるってことはフィッシュイーターはいないのかな。
牡蠣殻しか釣れなかったので、大人しくSOTOに向かうよ。見るからにSOTO。
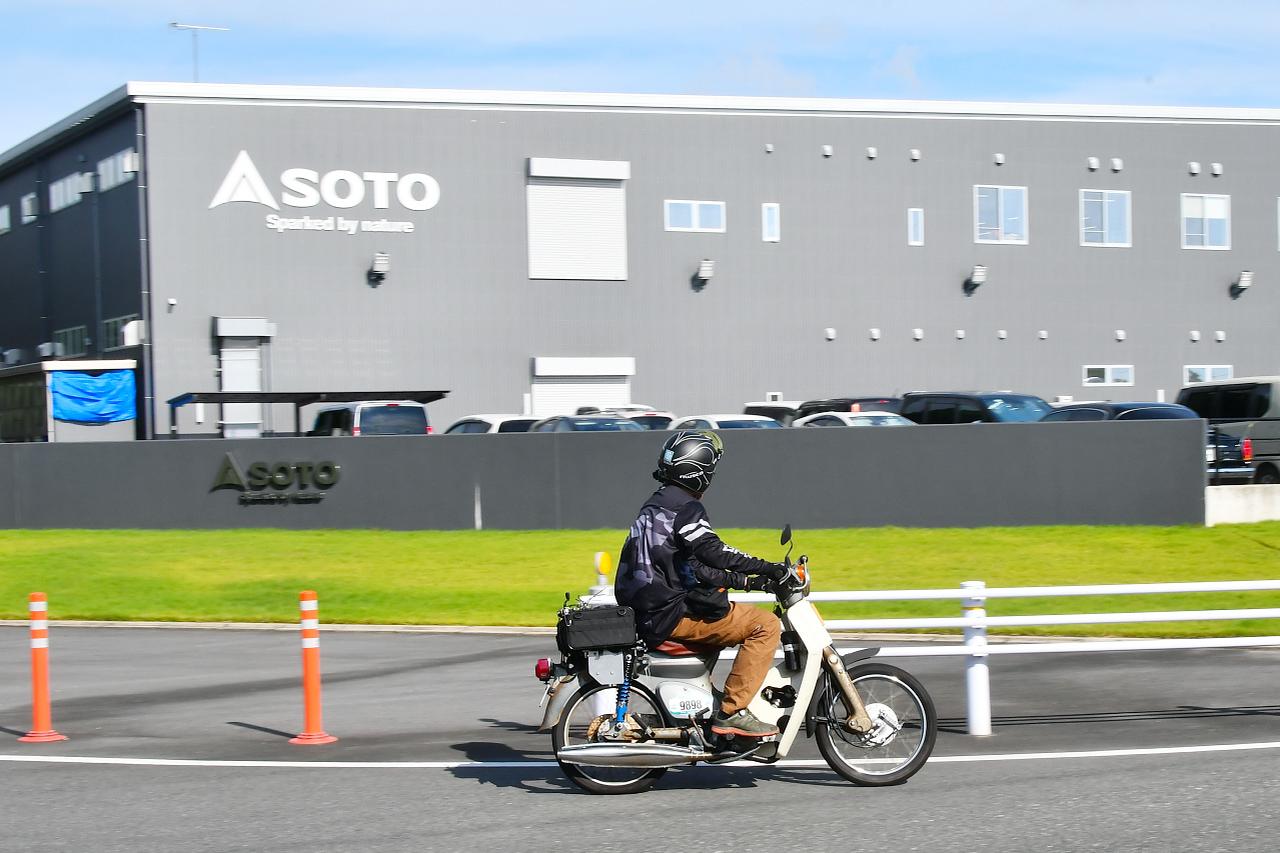
バーナーの心臓部はメイドイン東三河
敷地に入場。いや、久々のカブ90は楽しいね。
CT125・ハンターカブにはないダイレクト感が、すごく昭和で良い。
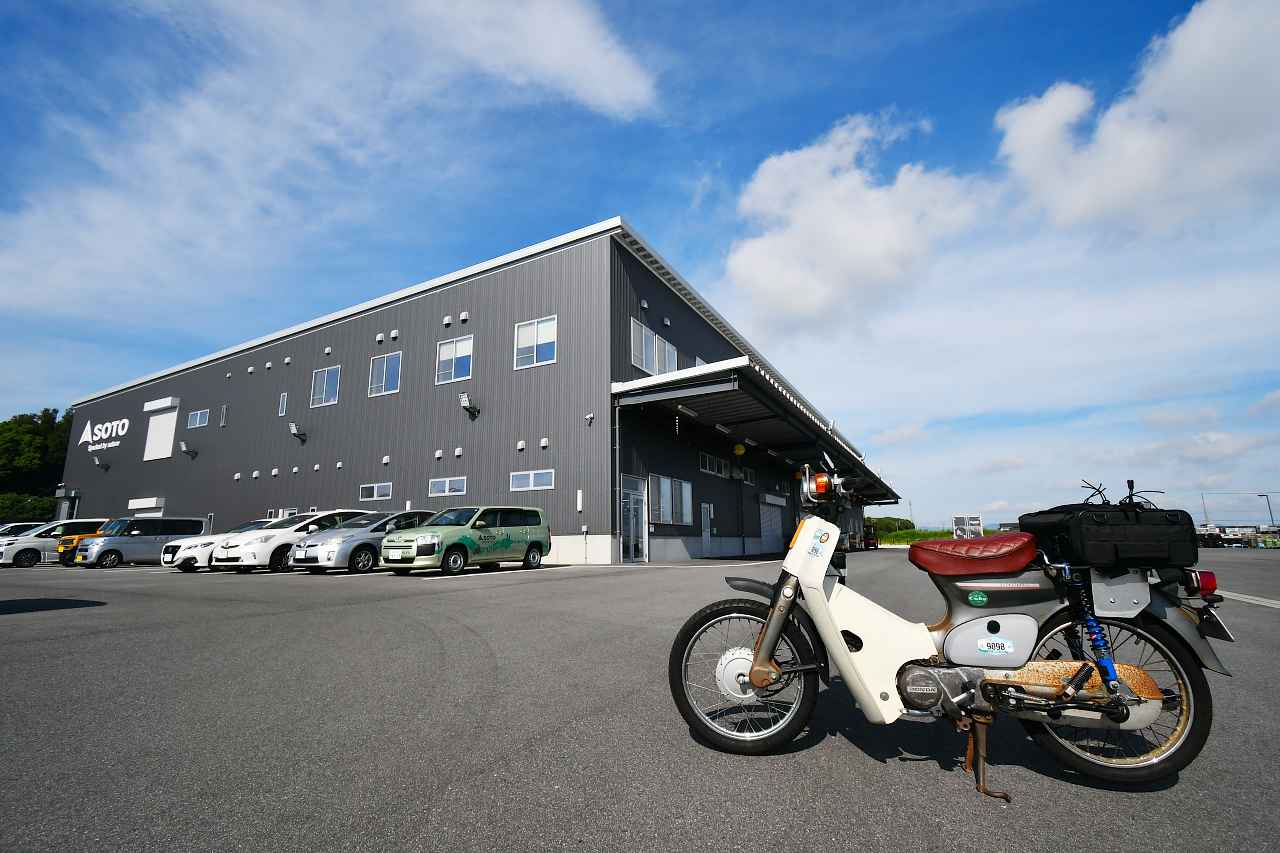
案内してくれるのはSOTO広報の坂之上さん。本日は宜しくお願いいたします。
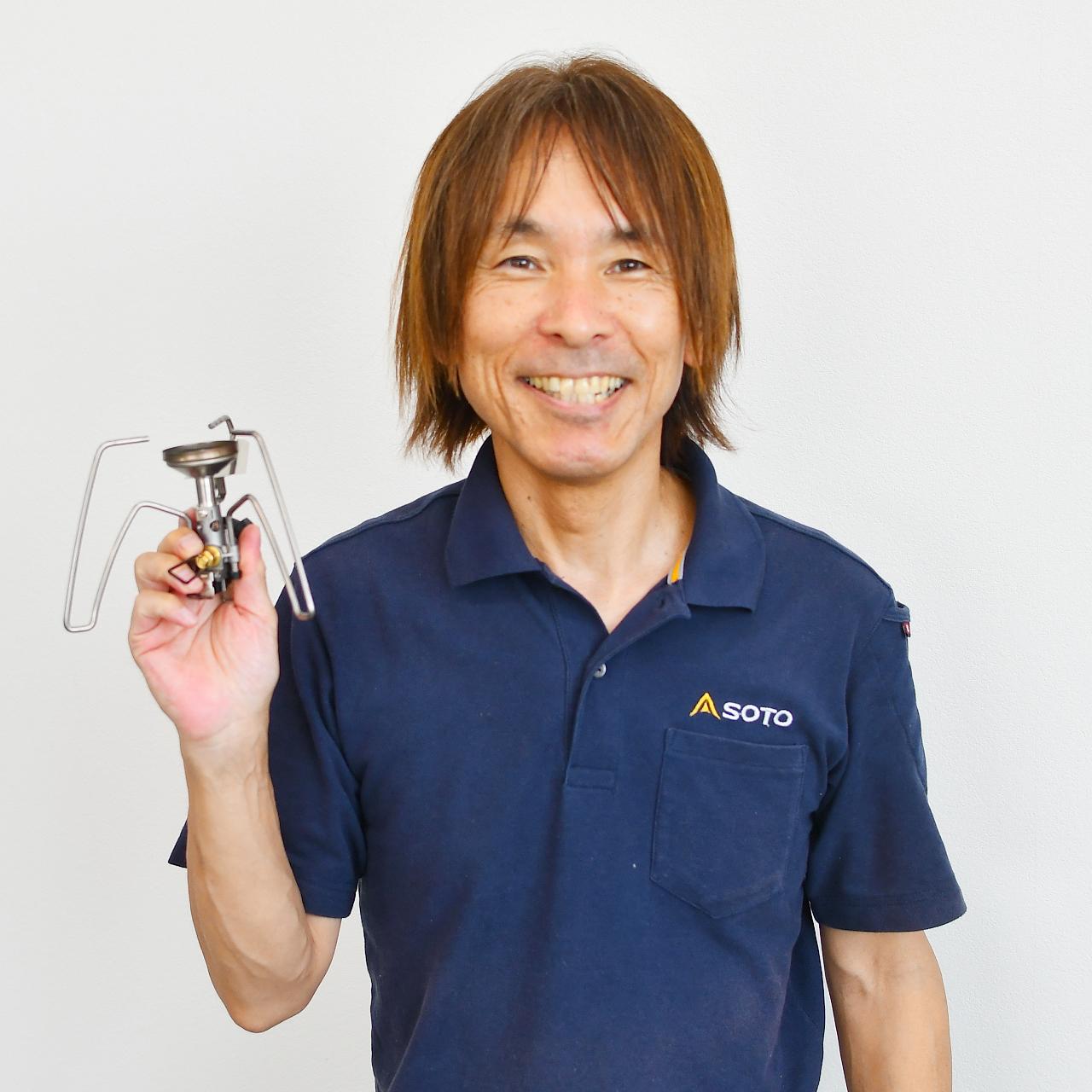
新富士バーナー株式会社
SOTO広報担当
坂之上さん
よろしくお願いします。
こちらでST-350とかストーブの生産をしているんですよね。
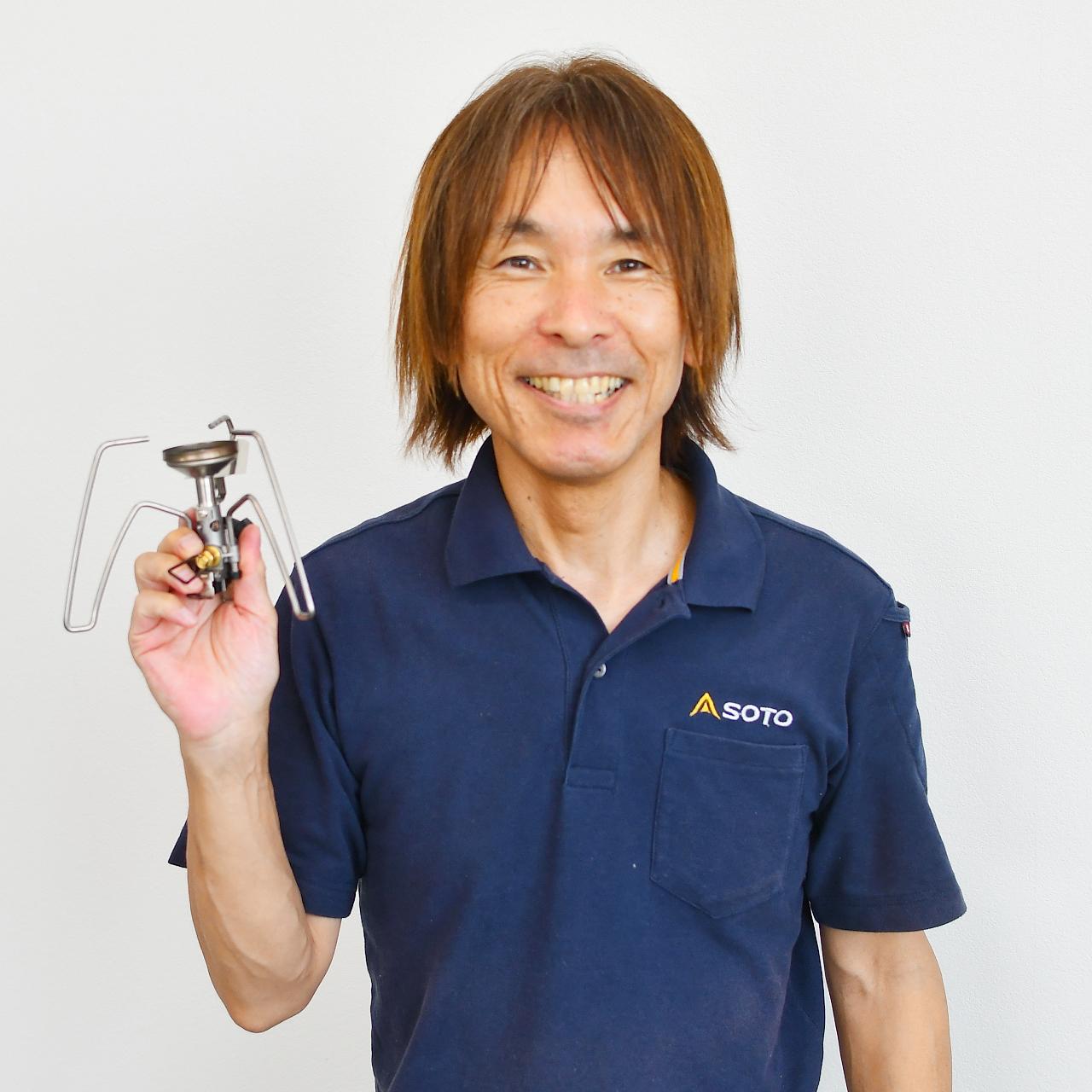
新富士バーナー株式会社
SOTO広報担当
坂之上さん
そうですね。ここは本社工場ということで、SOTO製品をはじめ、新富士バーナーのさまざまな燃焼器具の製造を行なっております。
そういえばSOTOブランドでテントとかもありますよね。なんとなくアウトドア総合メーカーというイメージがあるんですが。
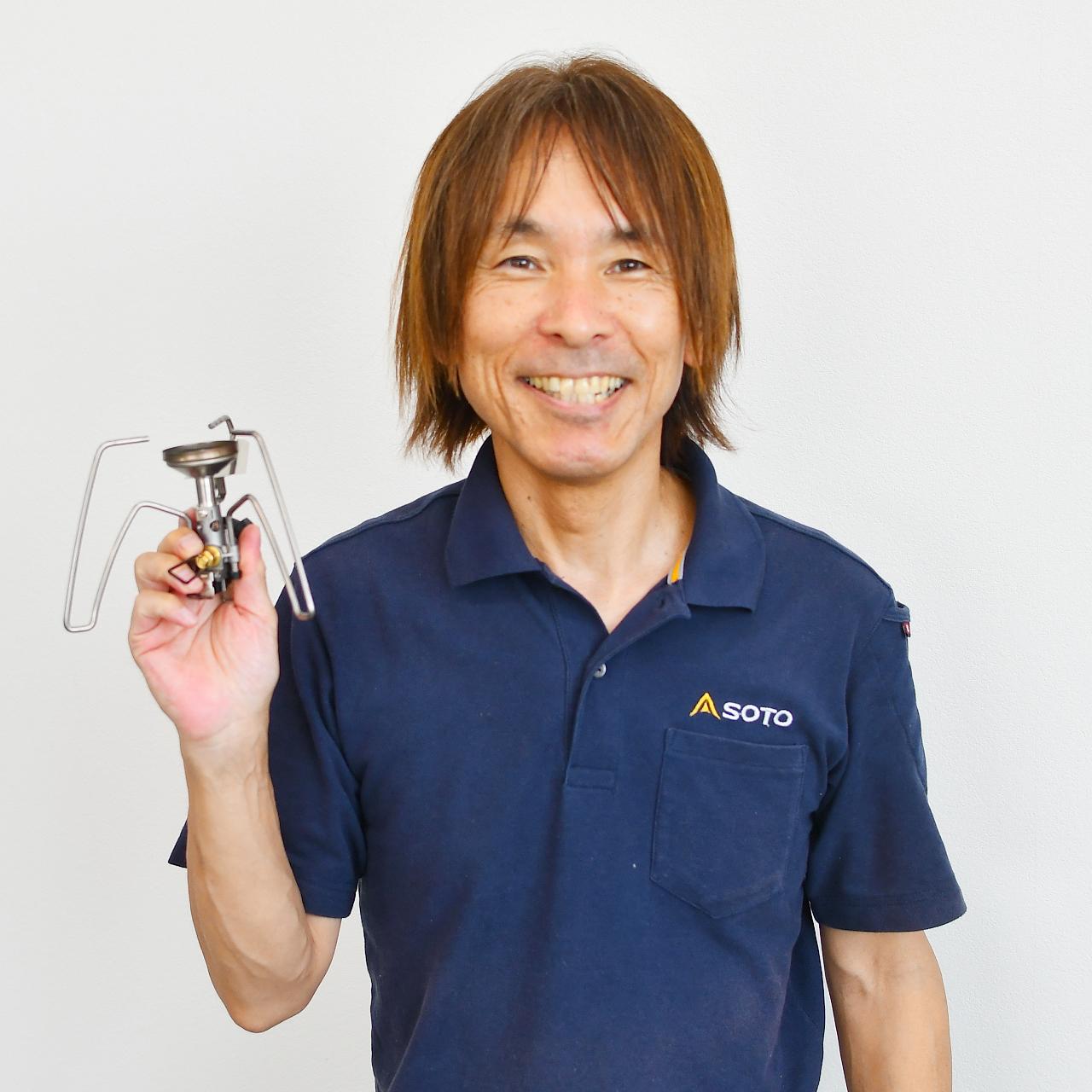
新富士バーナー株式会社
SOTO広報担当
坂之上さん
基本的に当社はバーナーやストーブなど、燃焼器具の専業メーカーというのが根底にあるんですよ。
テントやダッチオーブンなどもラインナップしていますが、それらは当社の燃焼器具に最適なテントや調理器具がなかったので、「それならば自社で作るしかない」ということで開発をしています。
ですので、あくまで燃焼器具メーカーであり、それらのアイテムは燃焼器具を活かすためのアイテムという位置づけになります。
なるほど、あくまで主役はバーナーとかストーブなんですね。
公式サイトを見ていたところ、ストーブ(バーナー)については全て日本製ってありました。全部この工場で作ってるんですか?
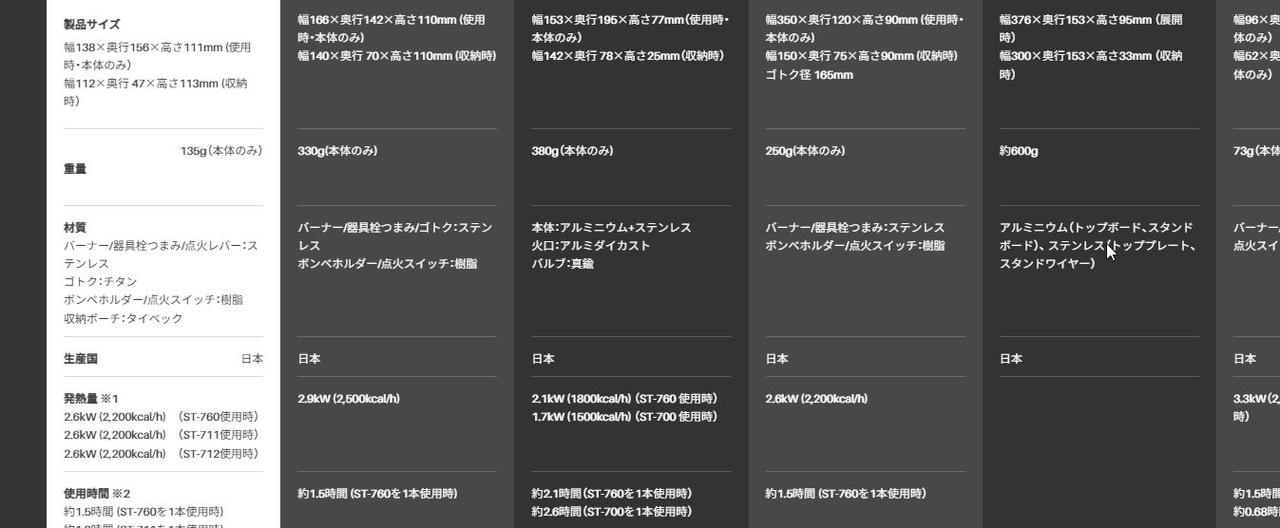
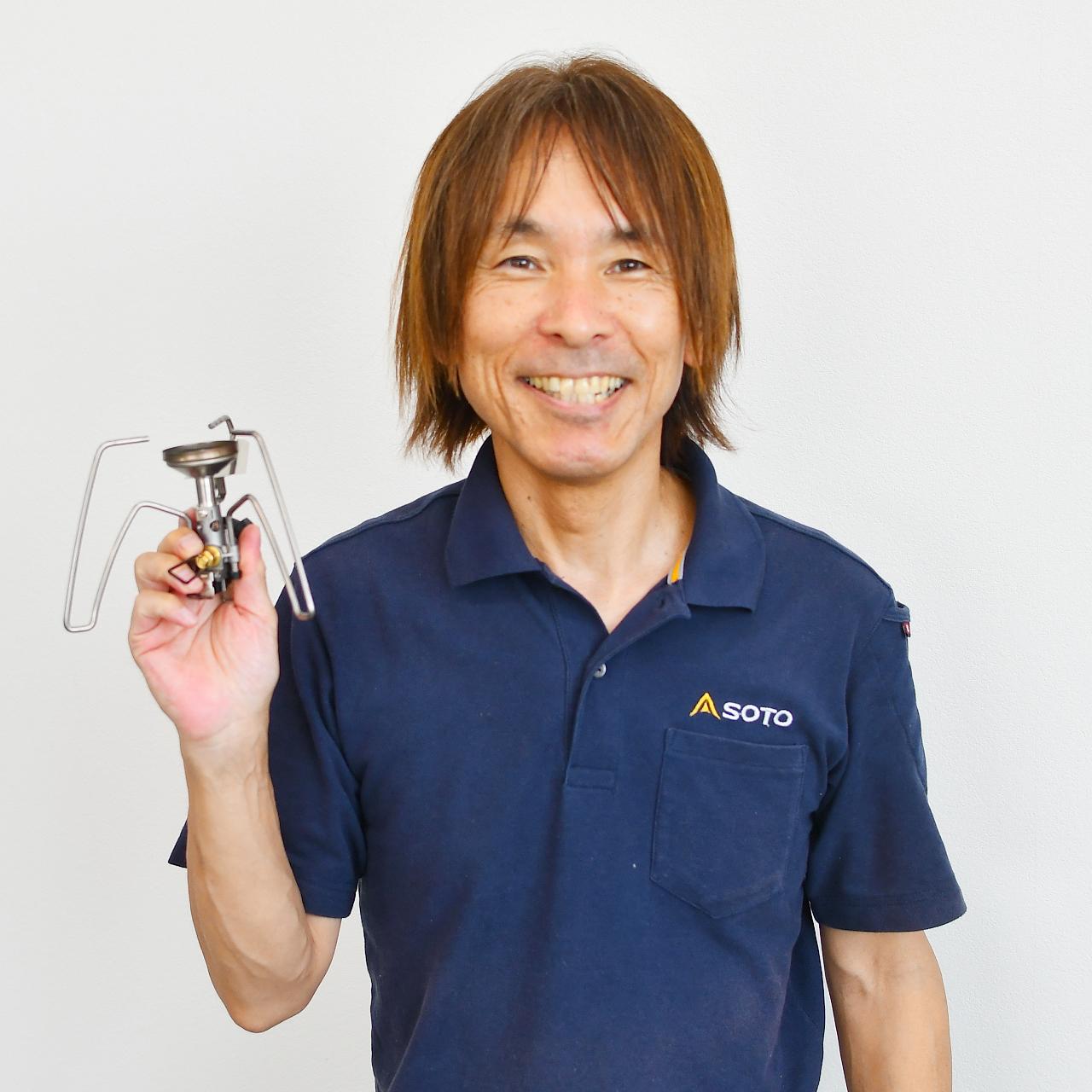
新富士バーナー株式会社
SOTO広報担当
坂之上さん
ゴトクや外装部などの一部部材については、豊川や豊川周辺の協力会社さんにお願いをしている部分もありますが、バーナーの心臓部についてはすべてここで生産しています。
なるほど、ということはメイドインジャパンというか、もはやメイドイン東三河なんですね。
ではさっそく工場を見ても良いでしょうか。
検査にはじまり検査に終わる。徹底っぷりが半端ない
まずは材料を加工して部材を作る生産工場。
超綺麗で掃除の徹底が凄い。機械の間も広くとられてて、作業効率良さそう。
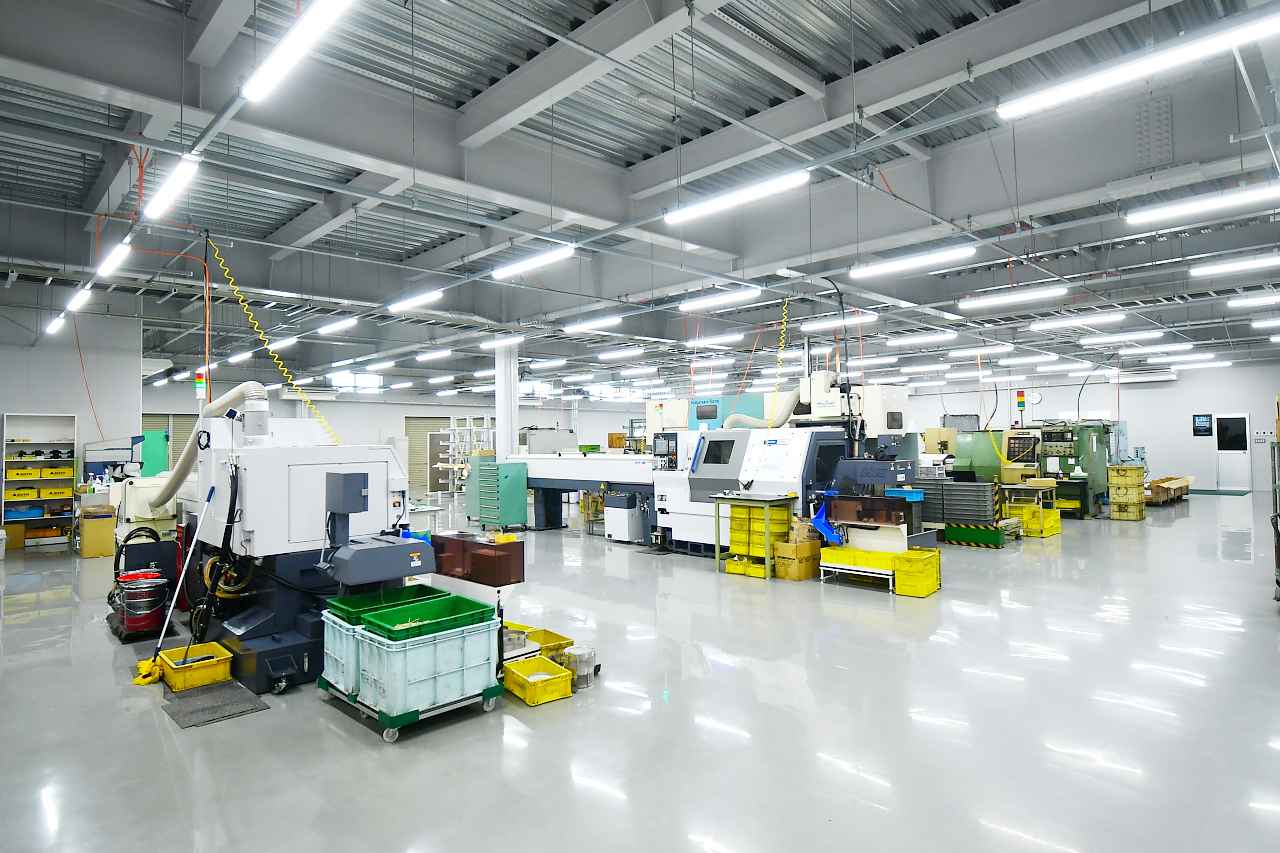
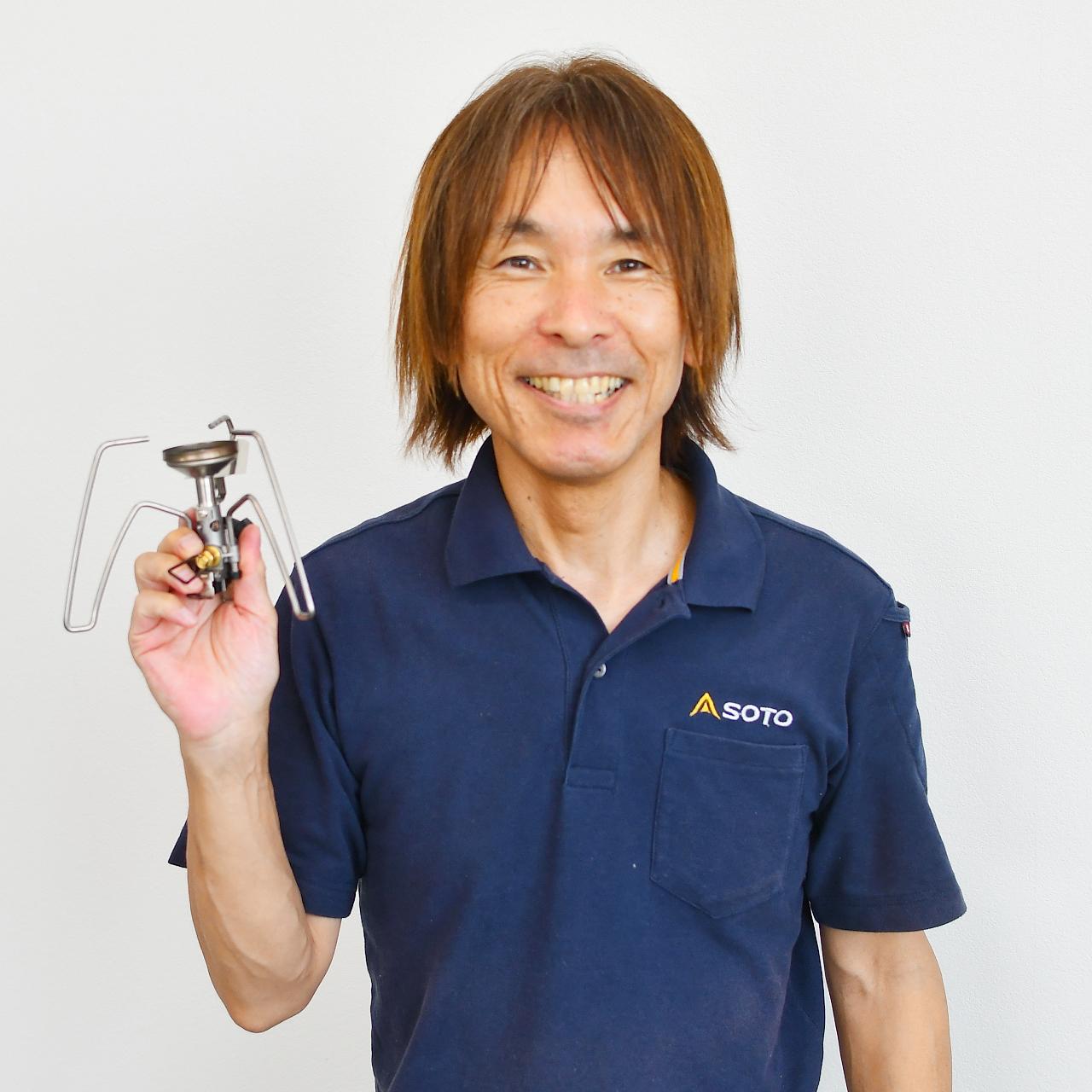
新富士バーナー株式会社
SOTO広報担当
坂之上さん
これらの工作機械は、24時間360日稼働しているんですよ。
5日だけお休みをとるんですね。
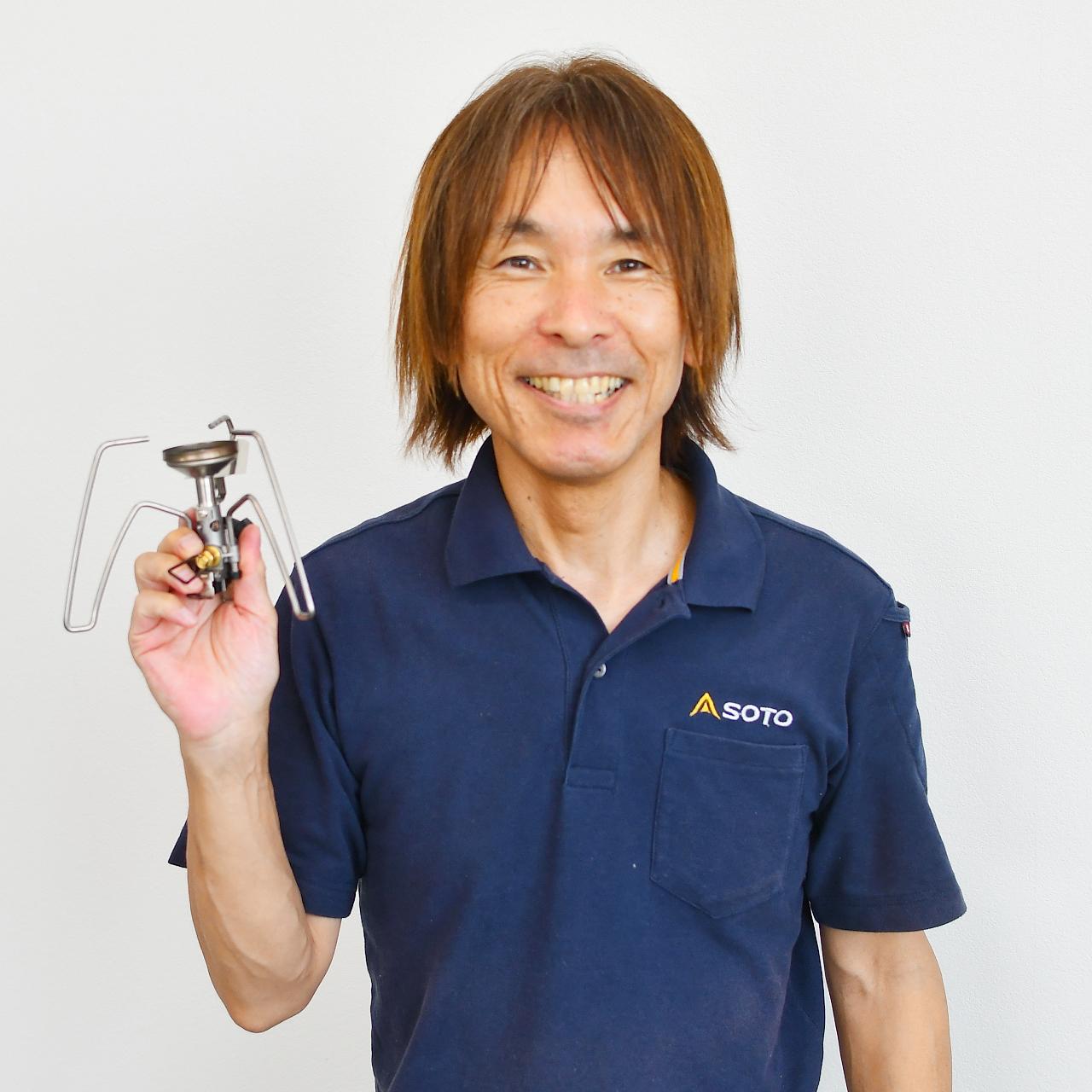
新富士バーナー株式会社
SOTO広報担当
坂之上さん
年末年始の5日間だけはお休みを頂いております。
それにしてもなんかやたらと綺麗ですね。
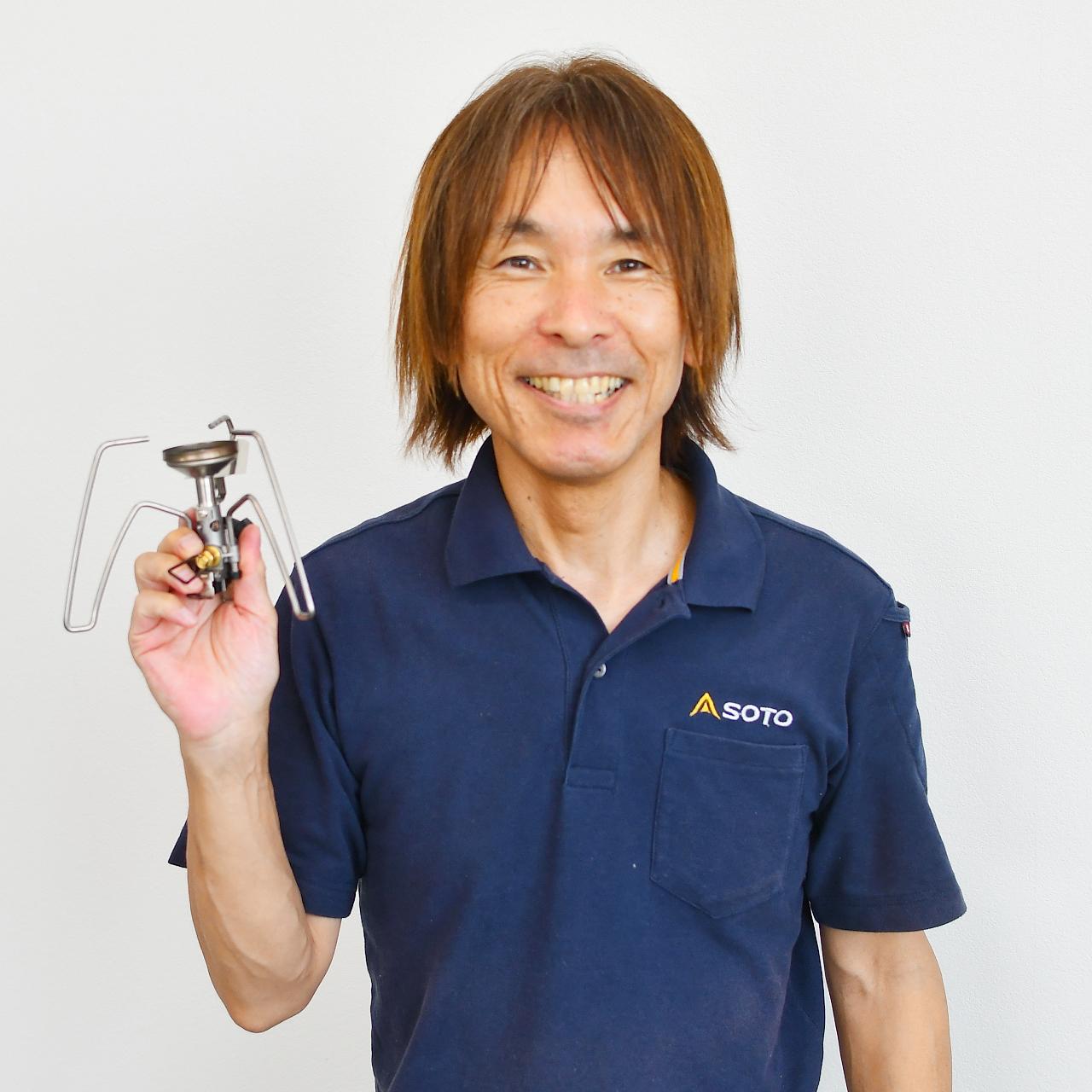
新富士バーナー株式会社
SOTO広報担当
坂之上さん
精密な加工や工作精度の高さを追求するためにも、綺麗な環境づくりは重要です。
どうしてもほこりなどは発生するので、清浄装置などを取り入れ99%くらいのほこりは自動で取り除いています。しかし、それでも1%は残るので、人の手による掃除も細かいサイクルで行なっています。
精度といえば、工作精度というか公差とかってどれくらいなんですか?
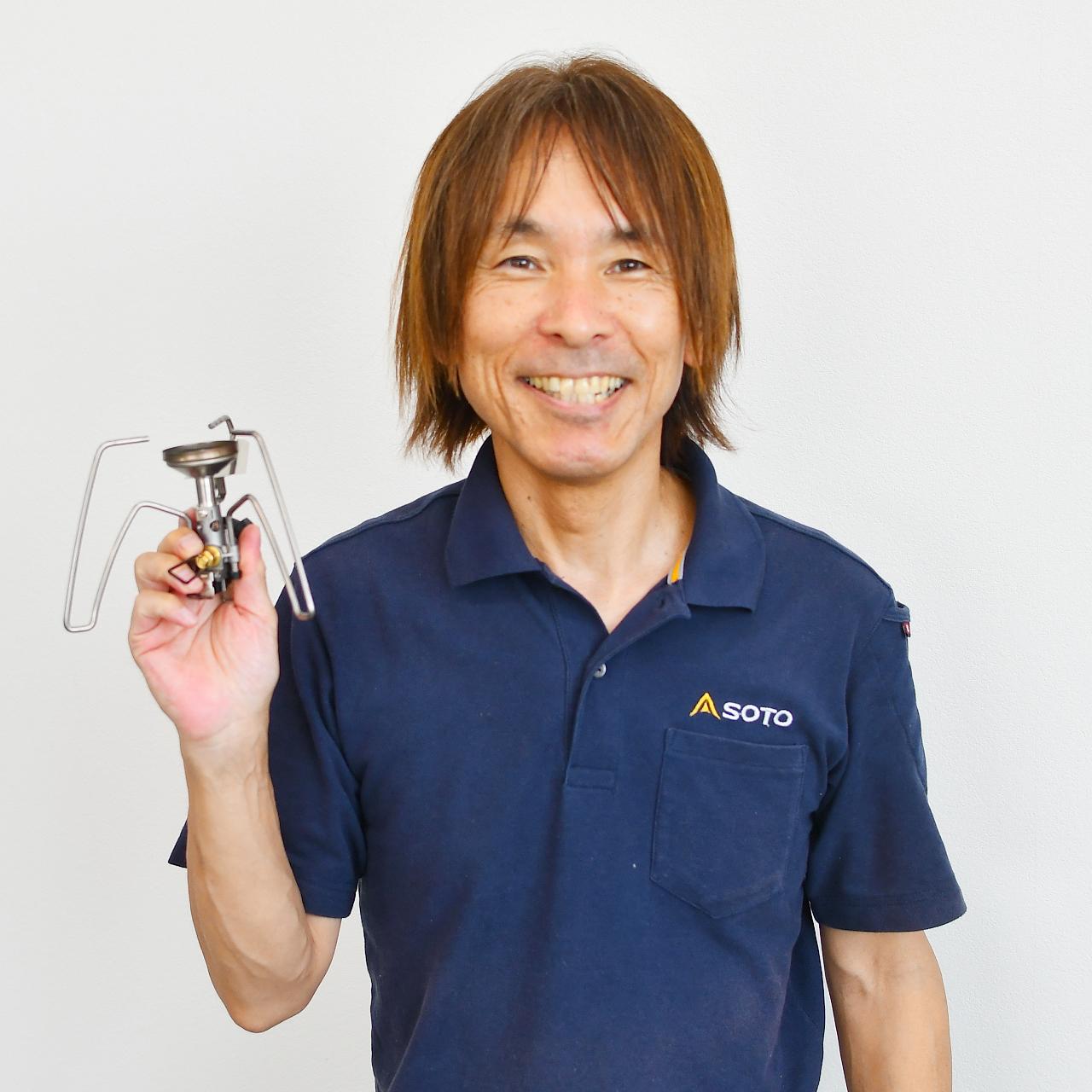
新富士バーナー株式会社
SOTO広報担当
坂之上さん
1/100ミリの中で管理をしています。
ですが、検査機械では1/1000まで測定できますし、1マイクロメートルでの精度を追求できる技術や検査制度を意識はしています。
なんというか、想像以上にすごいこだわりですね。
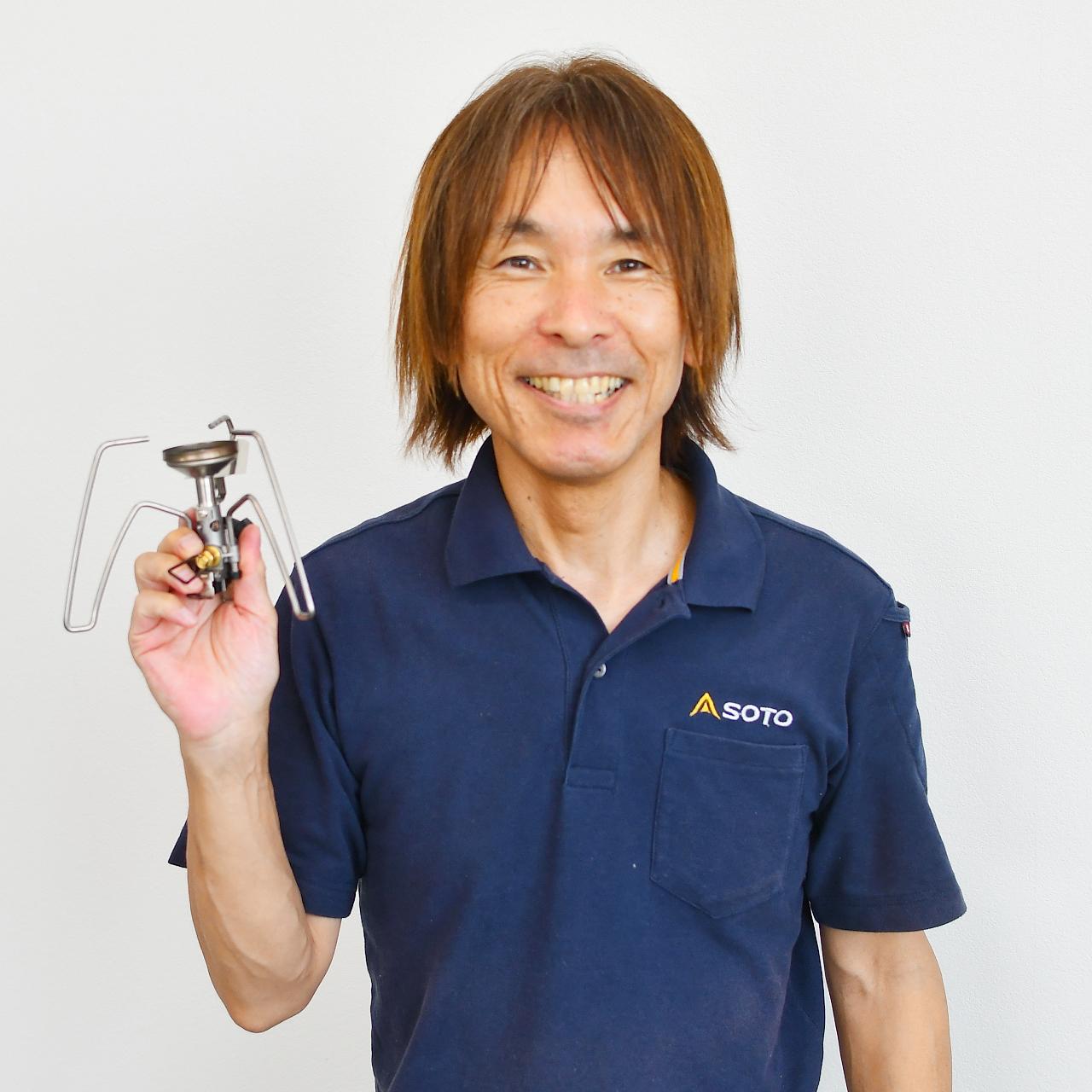
新富士バーナー株式会社
SOTO広報担当
坂之上さん
当社は基本的にバーナーの専業メーカーなので、第一に安全な炎をお客様に提供しなければなりません。
そのため徹底的に安全にこだわっているんですよ。
当社工場では、「徹底した検査」を最も重要視しています。
万が一の事故を防ぐためには、安定した工作精度の追求はもちろんですが、すべての製品を人間の手や目視で何工程も検査することで、ガス漏れや点火不具合などがないように徹底的にチェックしています。
なんとなくたくさん作る製品って抽出検査かと思ってましたが、一個ずつ全部検査してるんですね。大変そう。
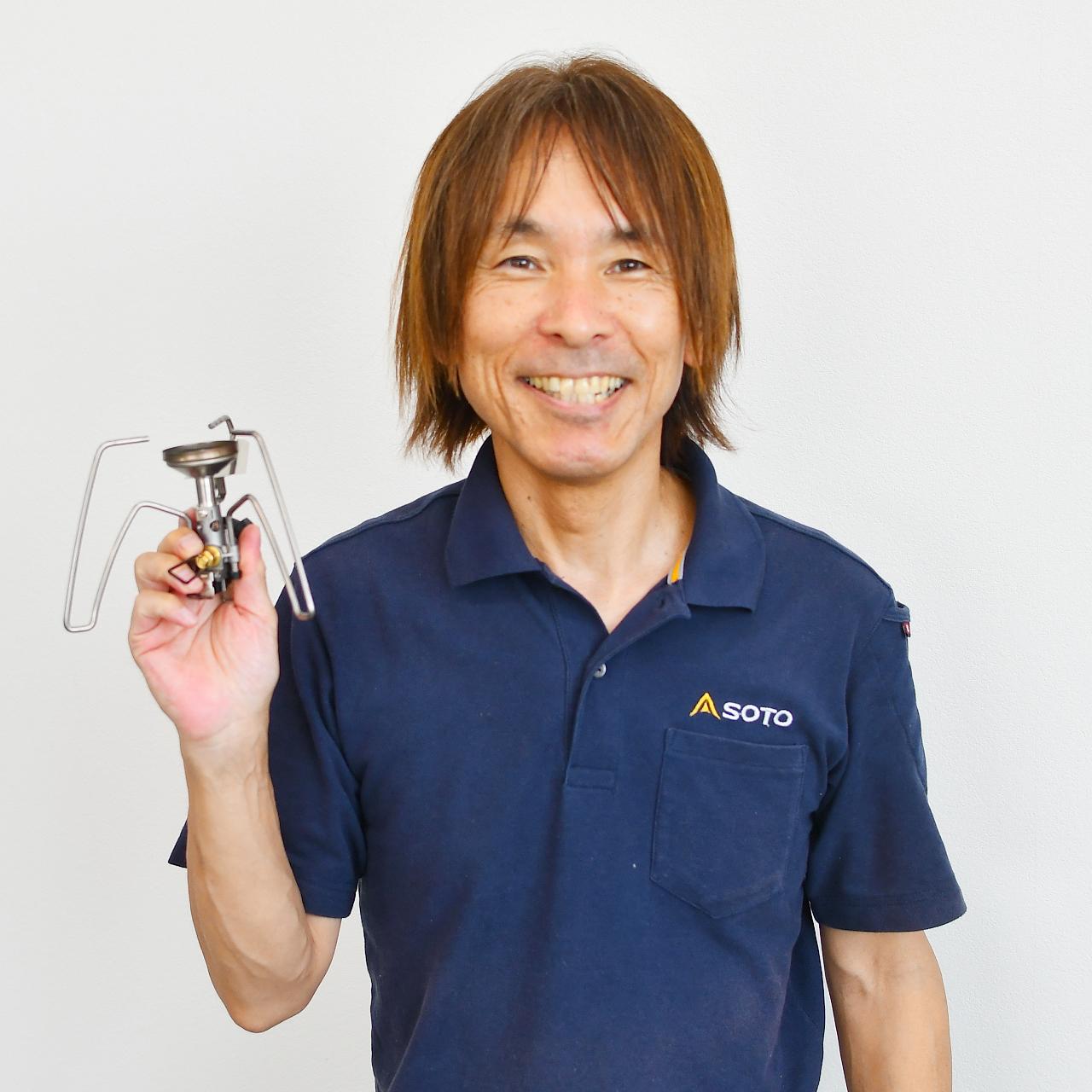
新富士バーナー株式会社
SOTO広報担当
坂之上さん
国内で販売されているガス器具には「◇PSLPG※」という認証もありますし、日本のガス器具のレベルは世界的にも非常に安全性が高いとは思います。
だからといって、そうした認証に甘えることなく、より厳しい基準で安全検査を徹底しています。
あとで見ていただきますが、普通ではやらないようなこだわった検査も行っていますよ。
※PSLPGには「◇PSLPG(ひし形PSLPG)」と「〇PSLPG(丸型PSLPG)」があり、各々意味が異なります。
◇PSLPGってあれですね、バーナー買ったときについてくるアルミ板に表記されてますね。
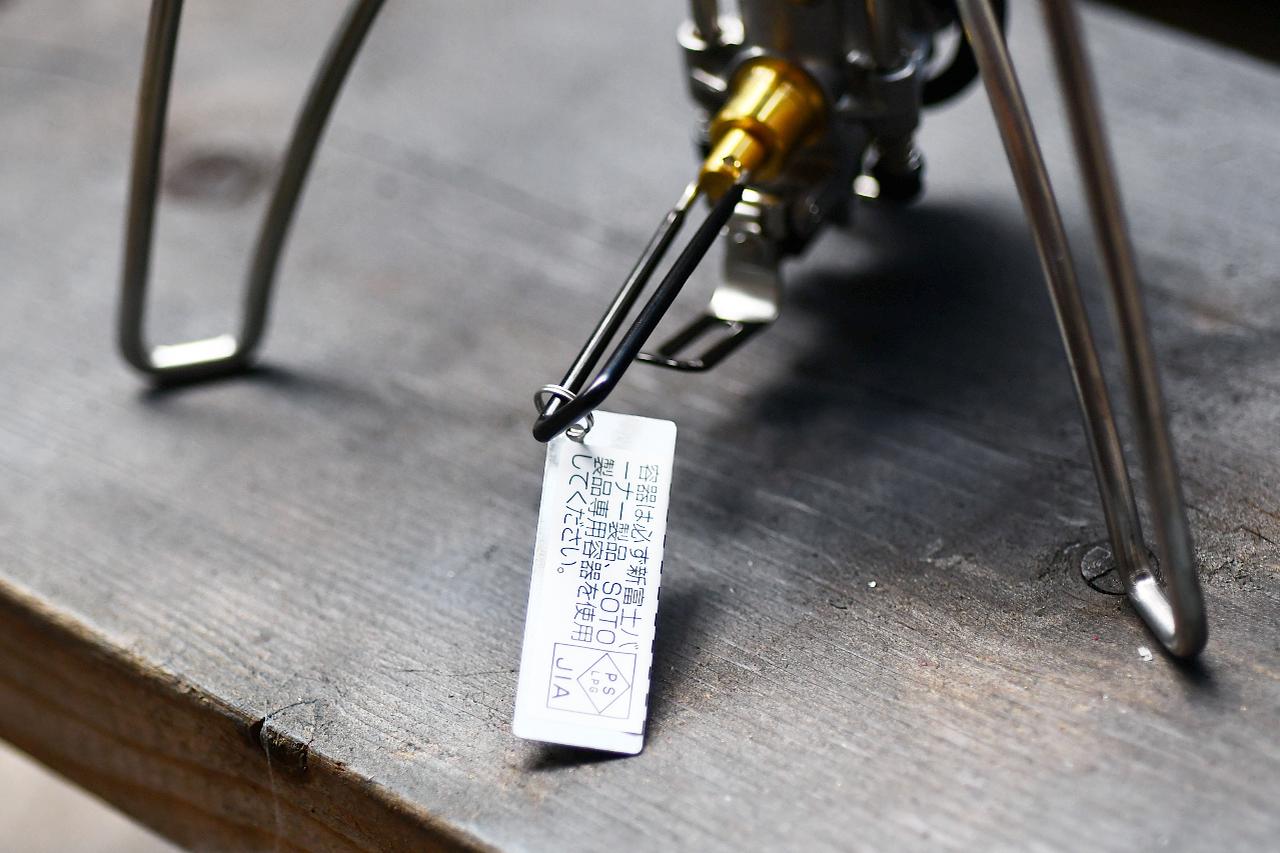
さっきamazonから届いたST-350TBの◇PSLPGラベル。
あれって使う時に外しちゃっても良いんですか?
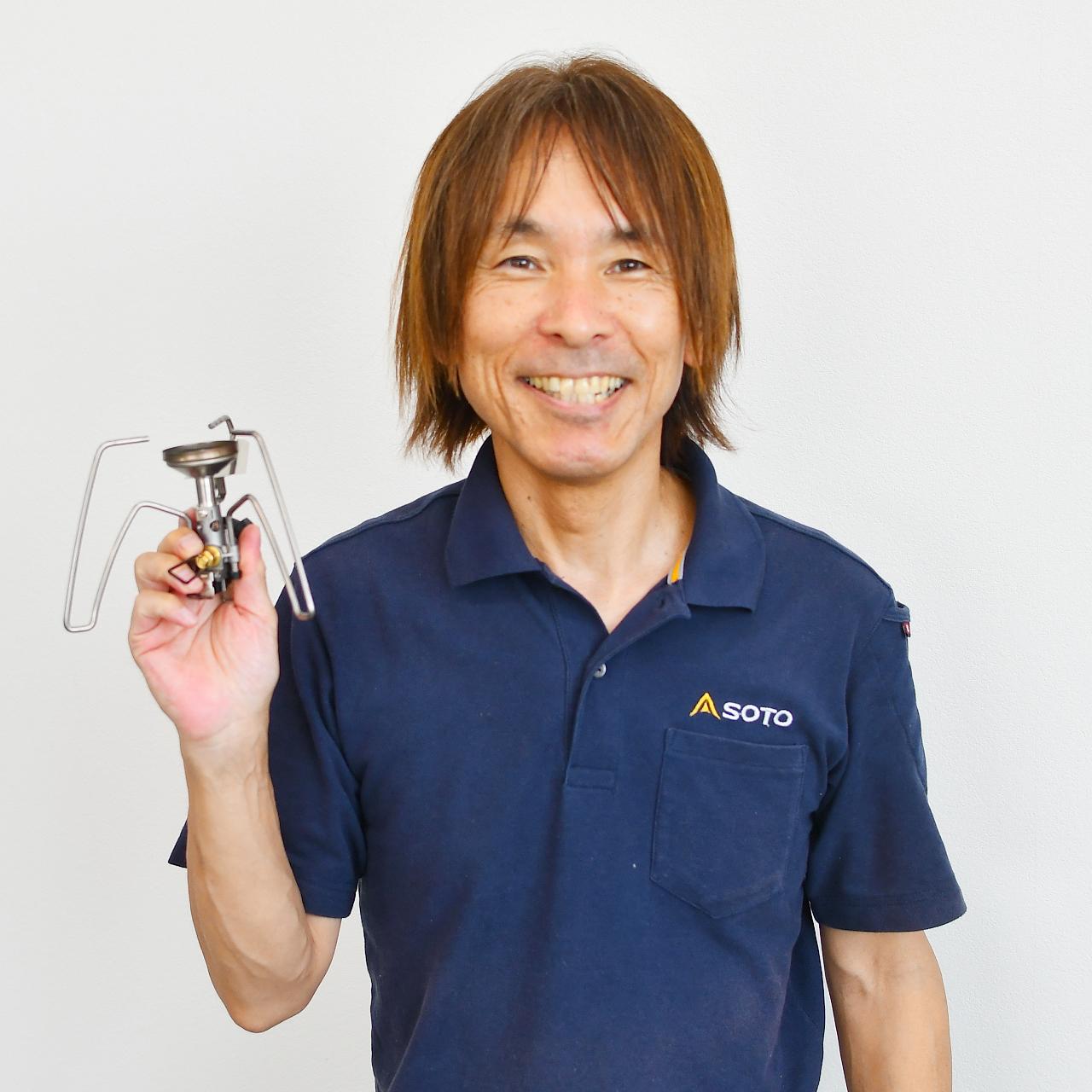
新富士バーナー株式会社
SOTO広報担当
坂之上さん
もちろん使用時には外していただいてもかまいませんよ。
ただ、ラベルについているロット番号は故障の際に商品情報を照会するのにもつかわれますので、外したラベルは大切に取っておいてくださいね。
なるほど了解。次からは取っときます!
加工&検査
まずは材料。これは真鍮材。他にもステンレスとかアルミとか。それらがなんやかやしてバーナーの心臓部になるよ。
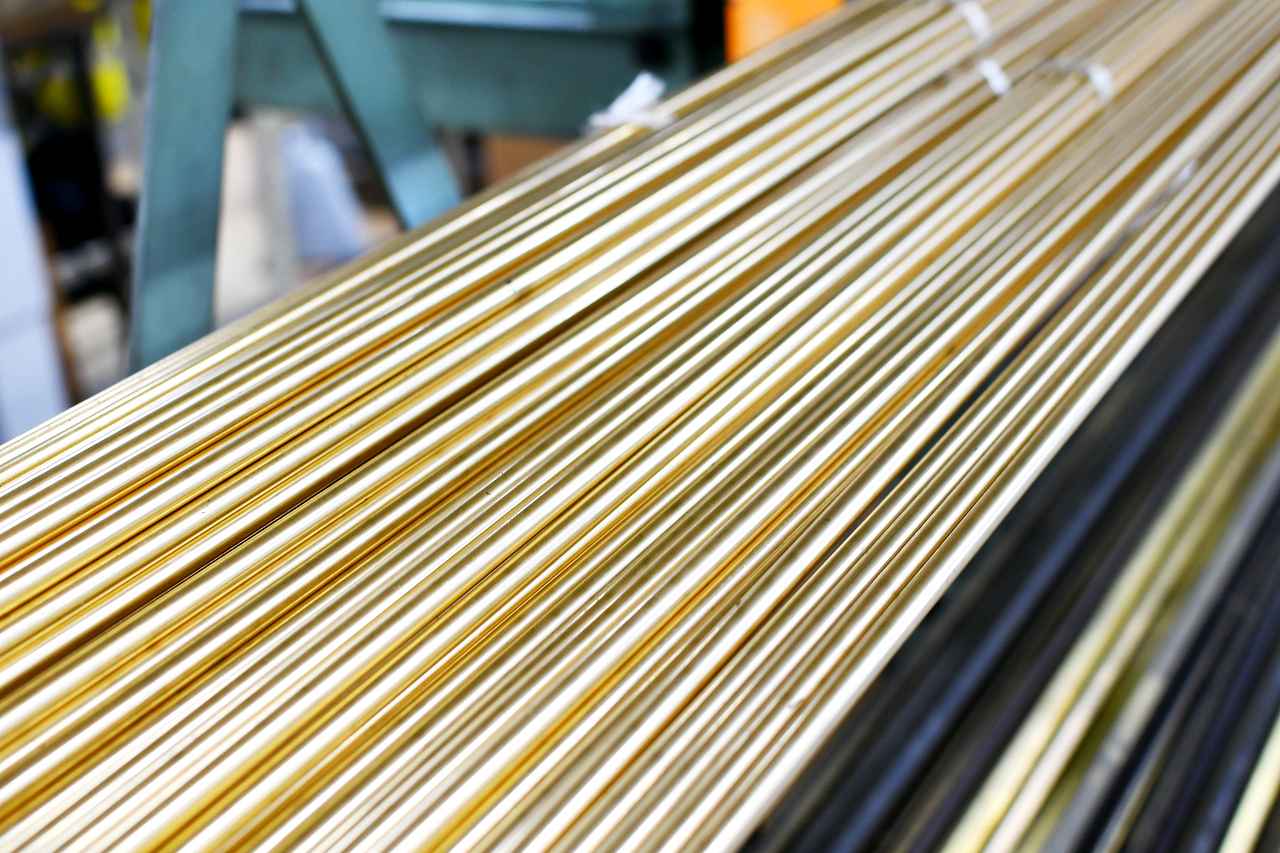
こうした材料を、NC工作機などで削ったり、掘ったりして加工。
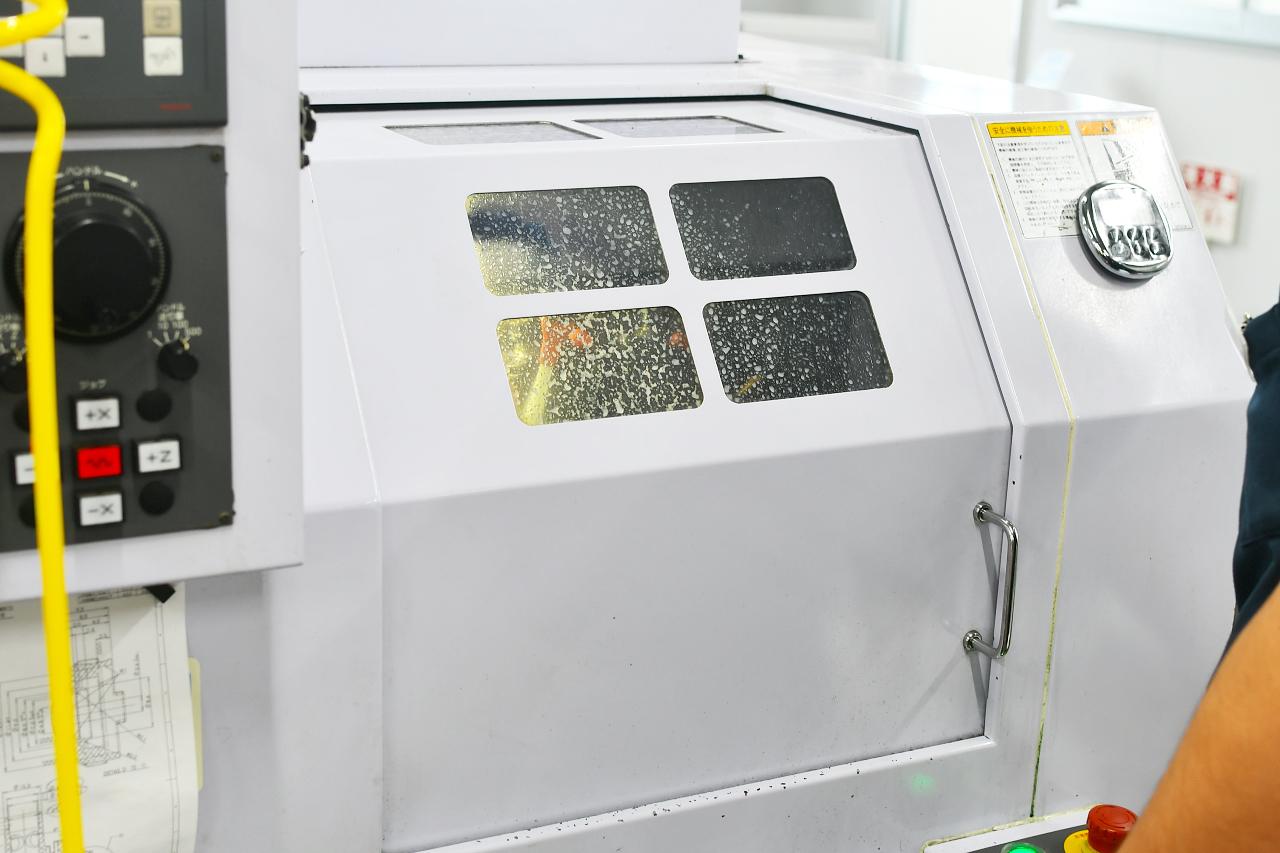
NC工作機には旋盤やフライス盤、研削盤なんかがあって、工程によってさまざまな機械を駆使していくよ。
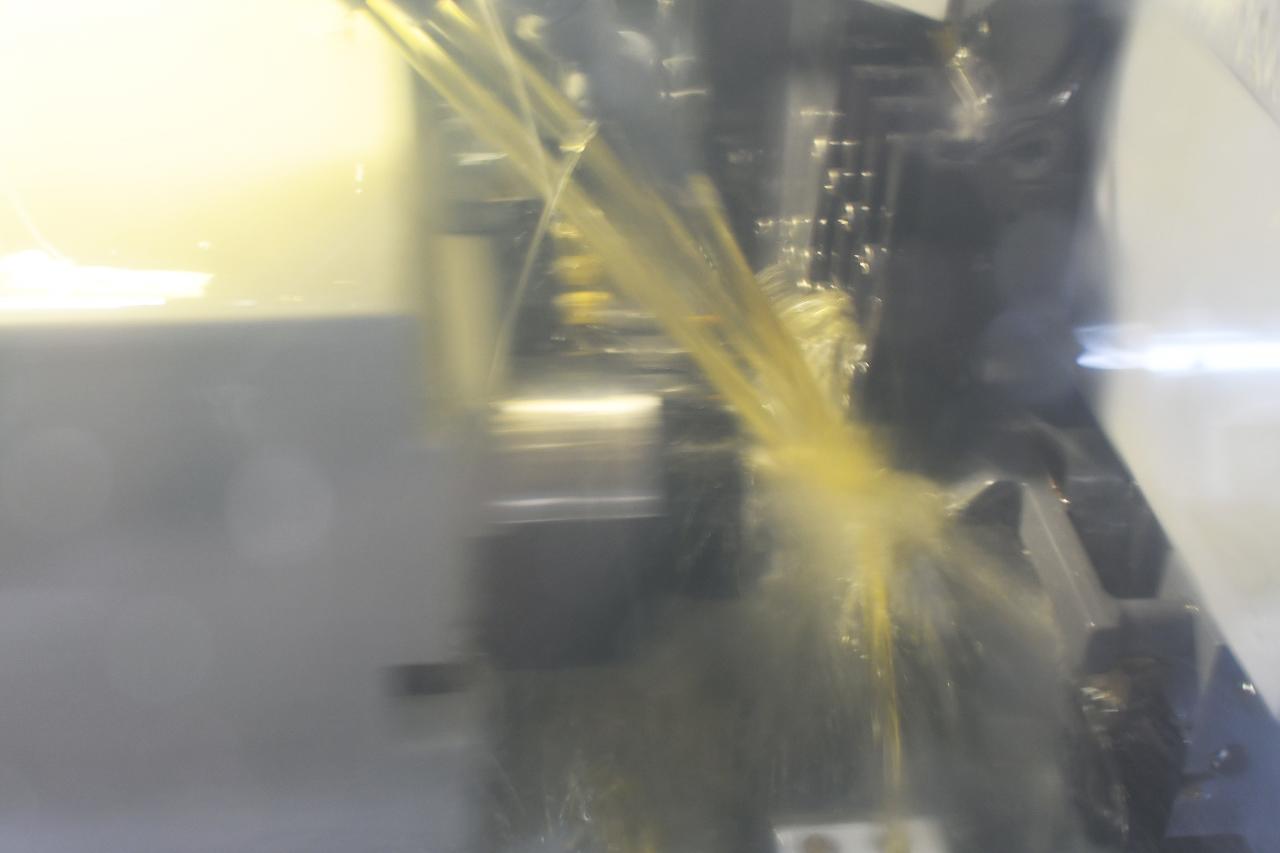
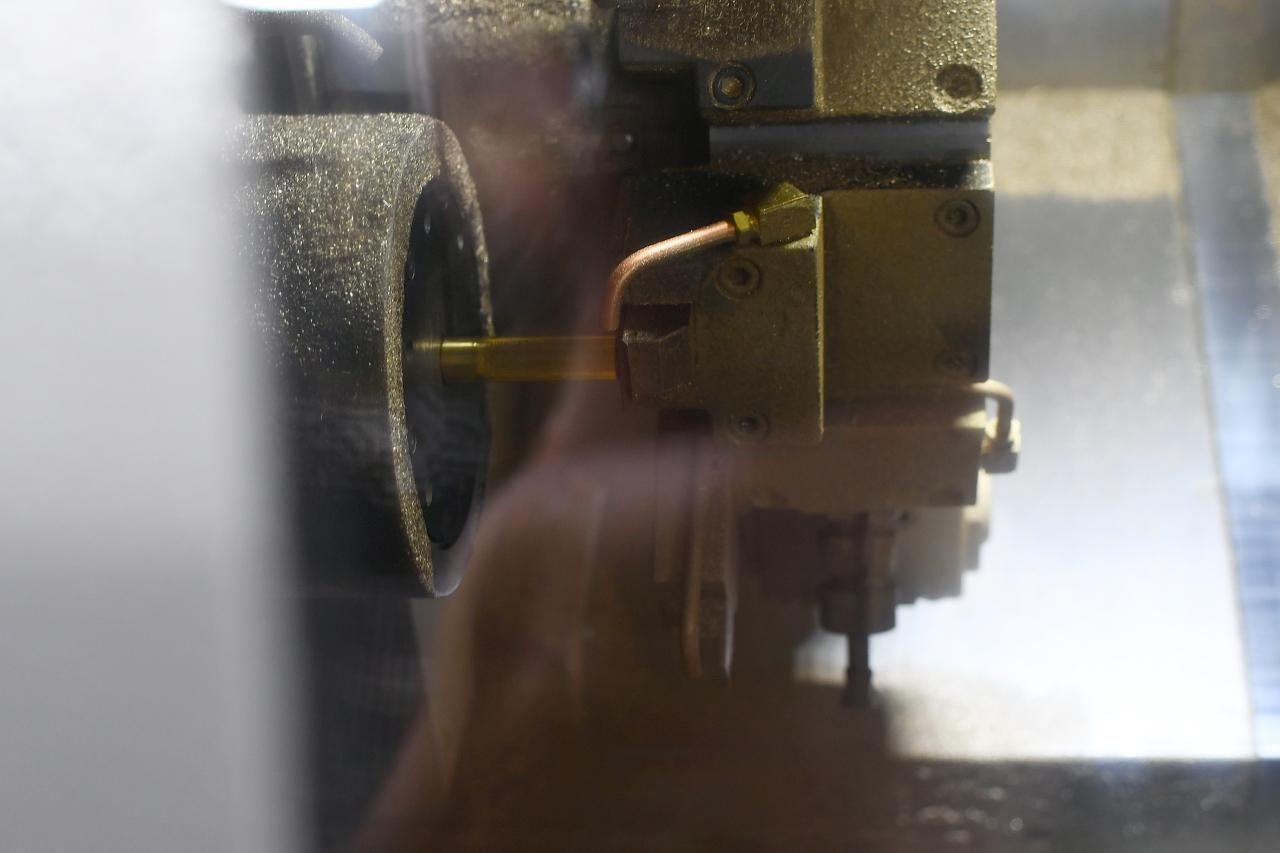
こういう複雑な形状のものは複数軸のマシニングセンタなんかも活用。
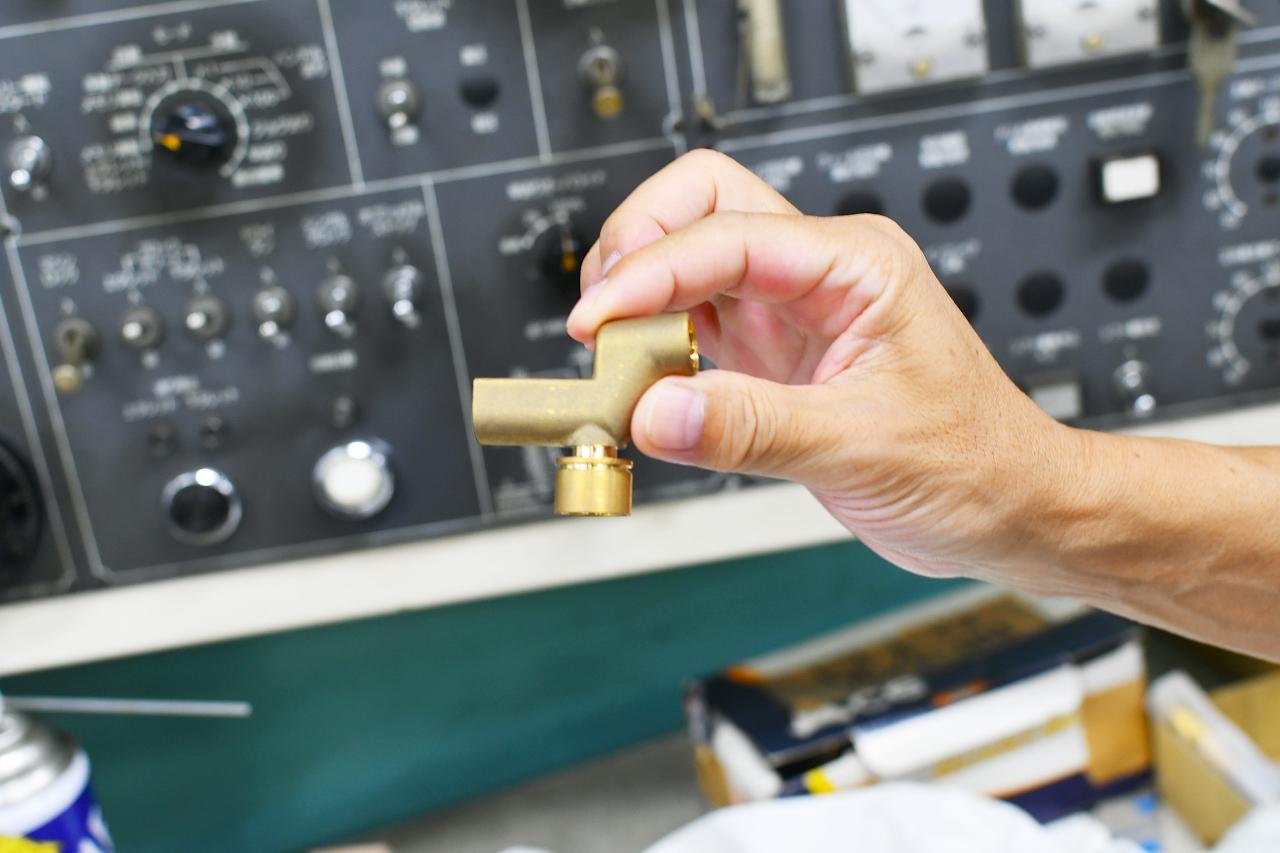
工場の機械を見てると、自分がこれまでに見た工場の機械とはちょっと雰囲気が違う感じ。
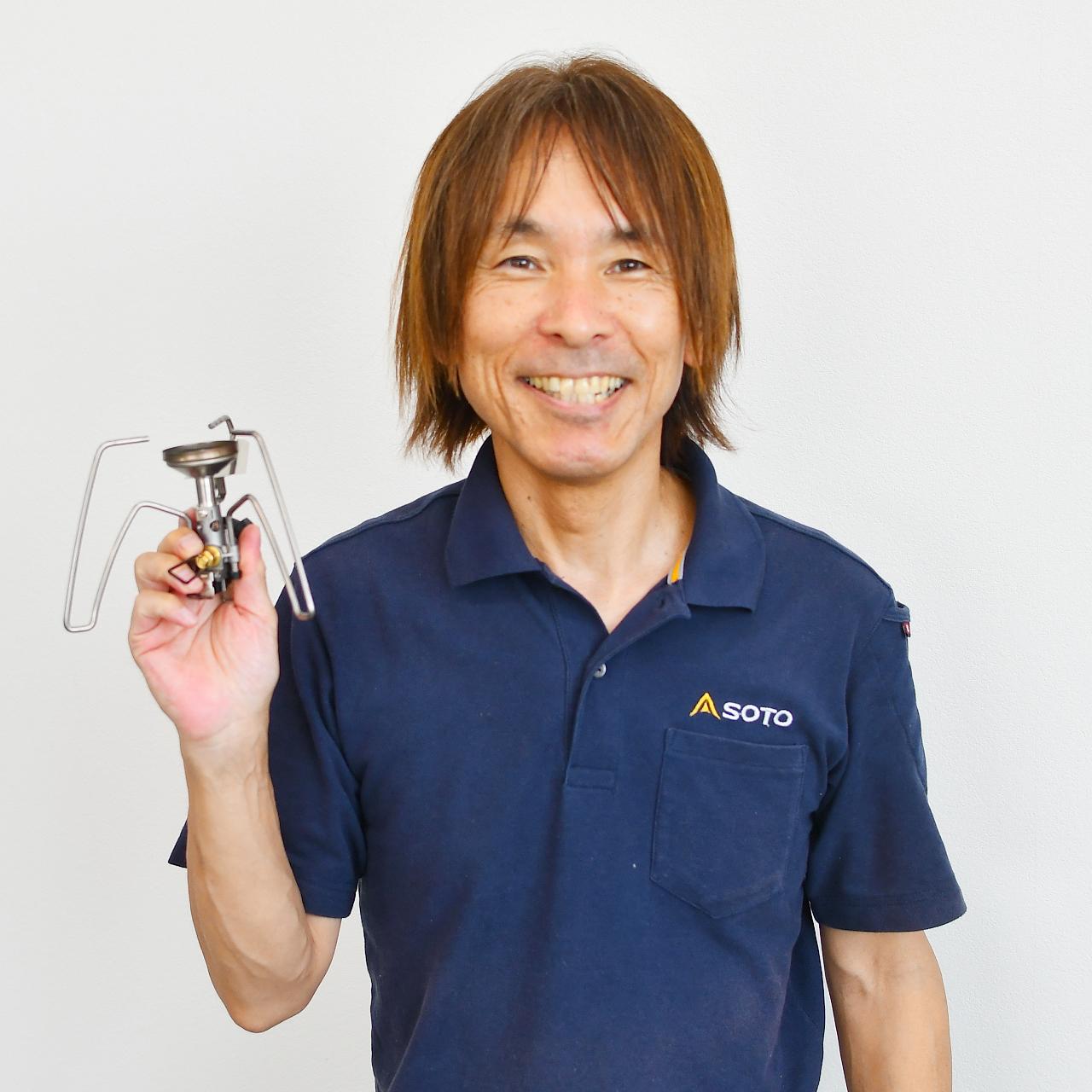
新富士バーナー株式会社
SOTO広報担当
坂之上さん
コンパクトで精密な機構を製造するということで、そうした作業に適した精度を追求した機械を選んでいます。
なるほど。たしかに出来上がった部品を見てると相当小さい。
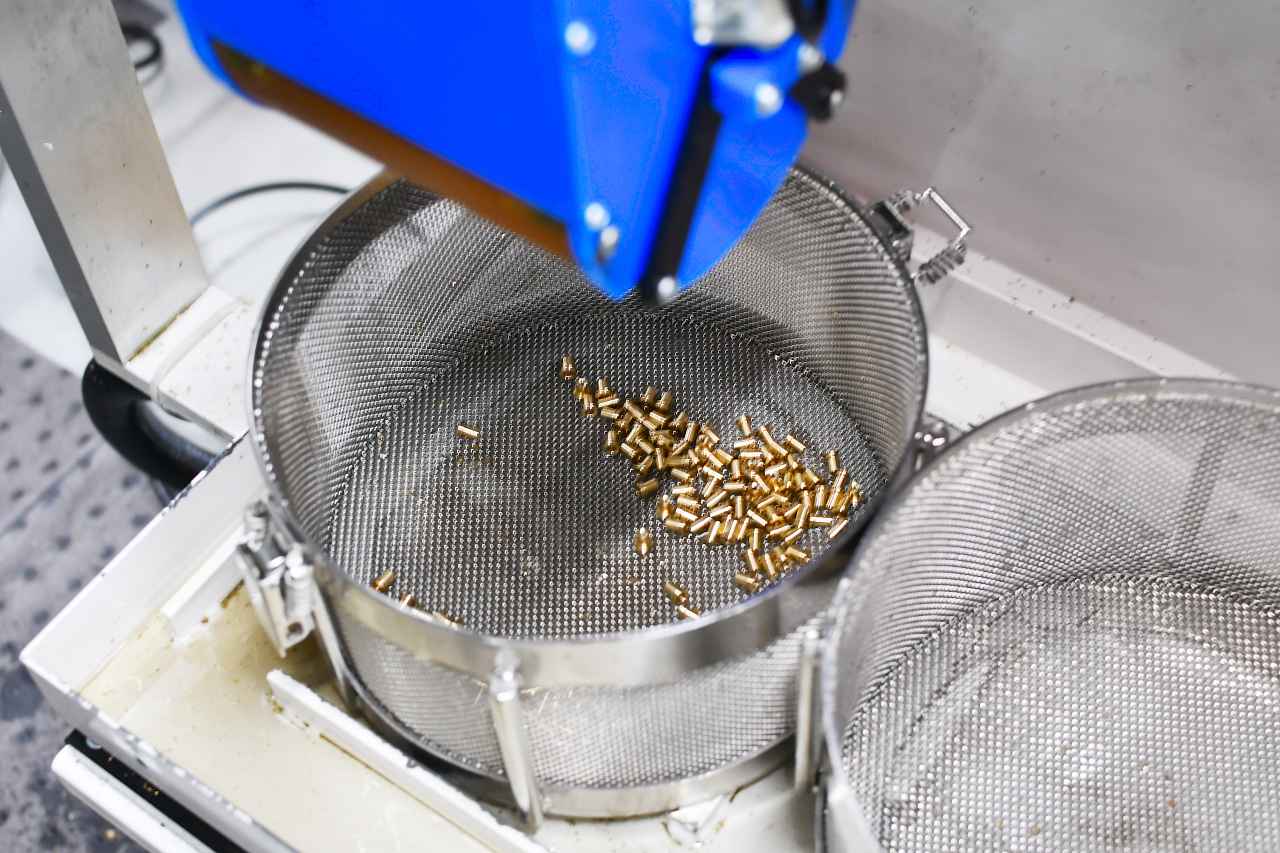
NCだけじゃなく、プレスによる加工も行なってるよ。
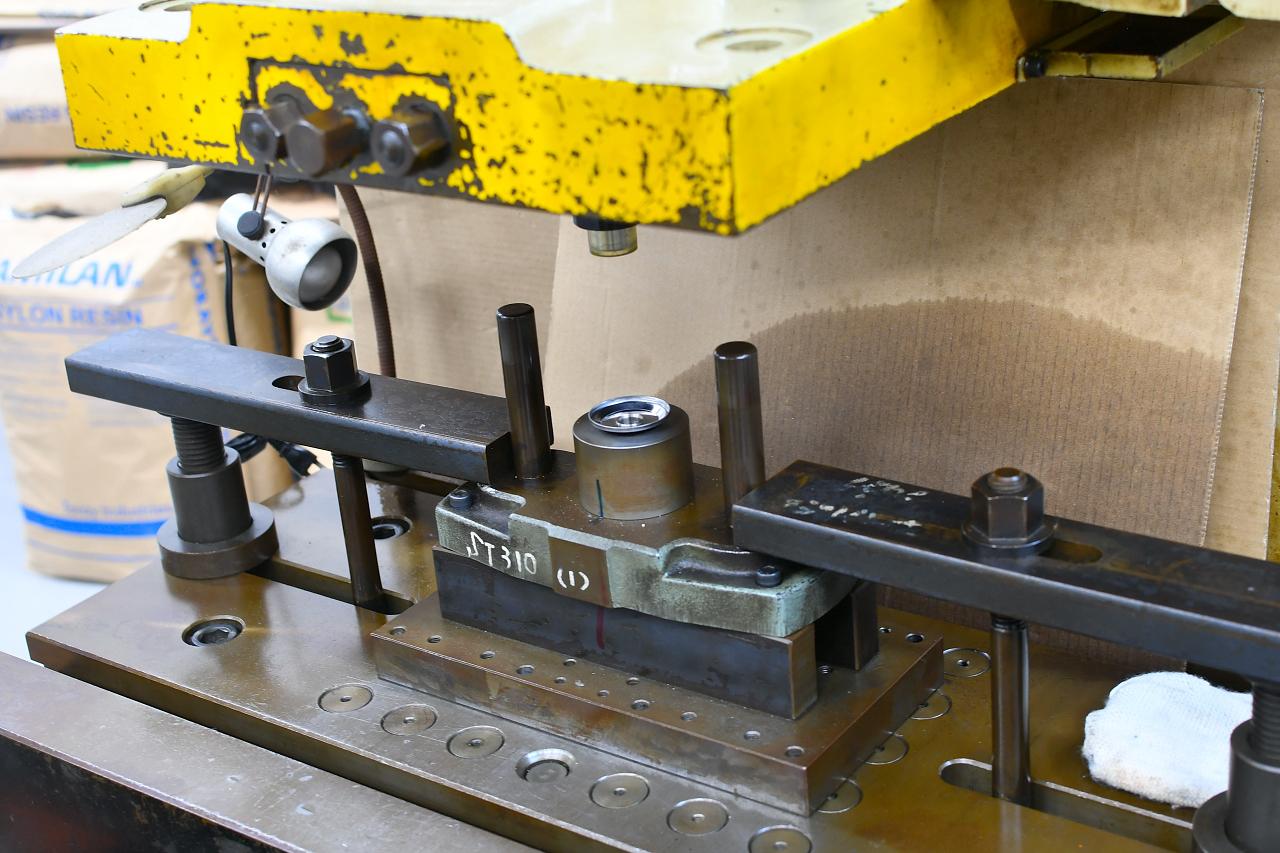
そういえば、あっちこっちに検査器具が。
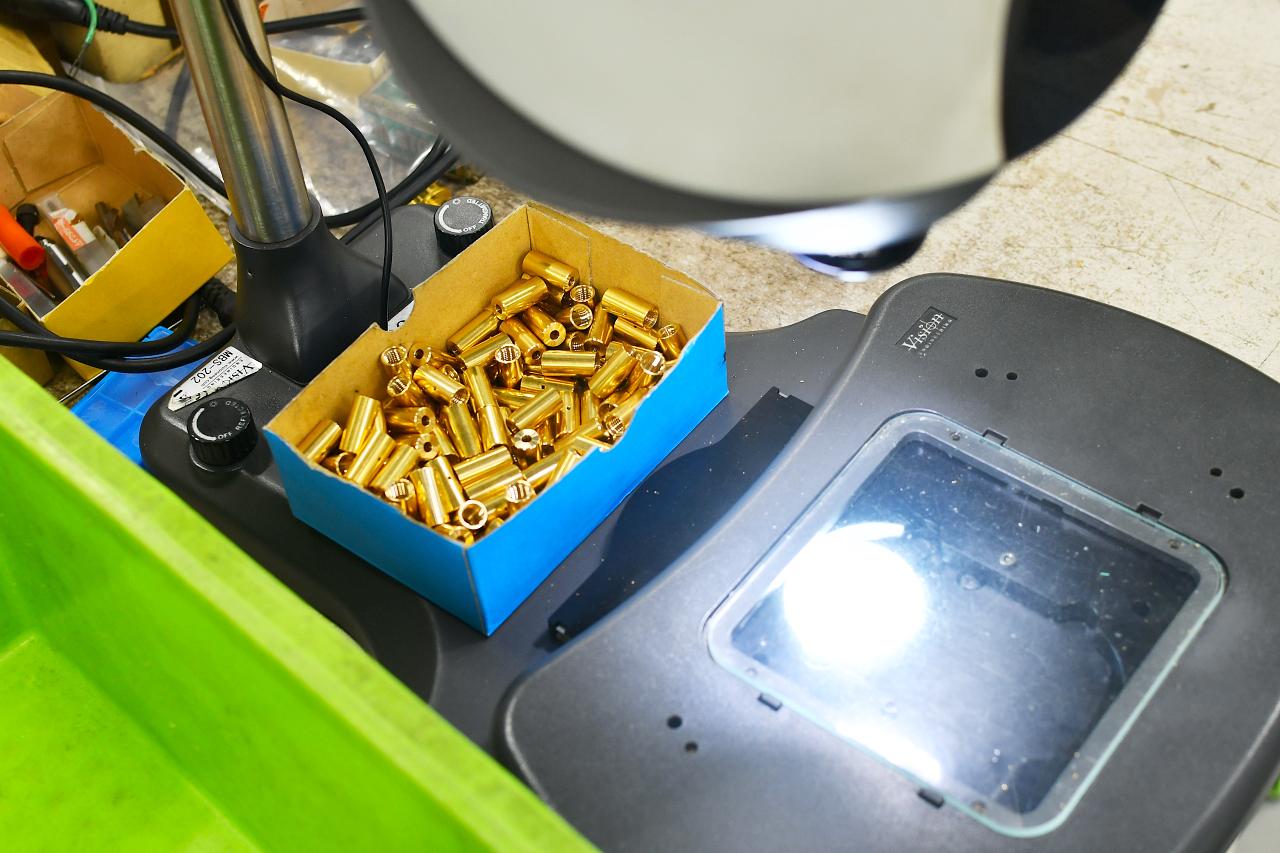
これ、もしかして部材ができるごとに検査してるんですか?
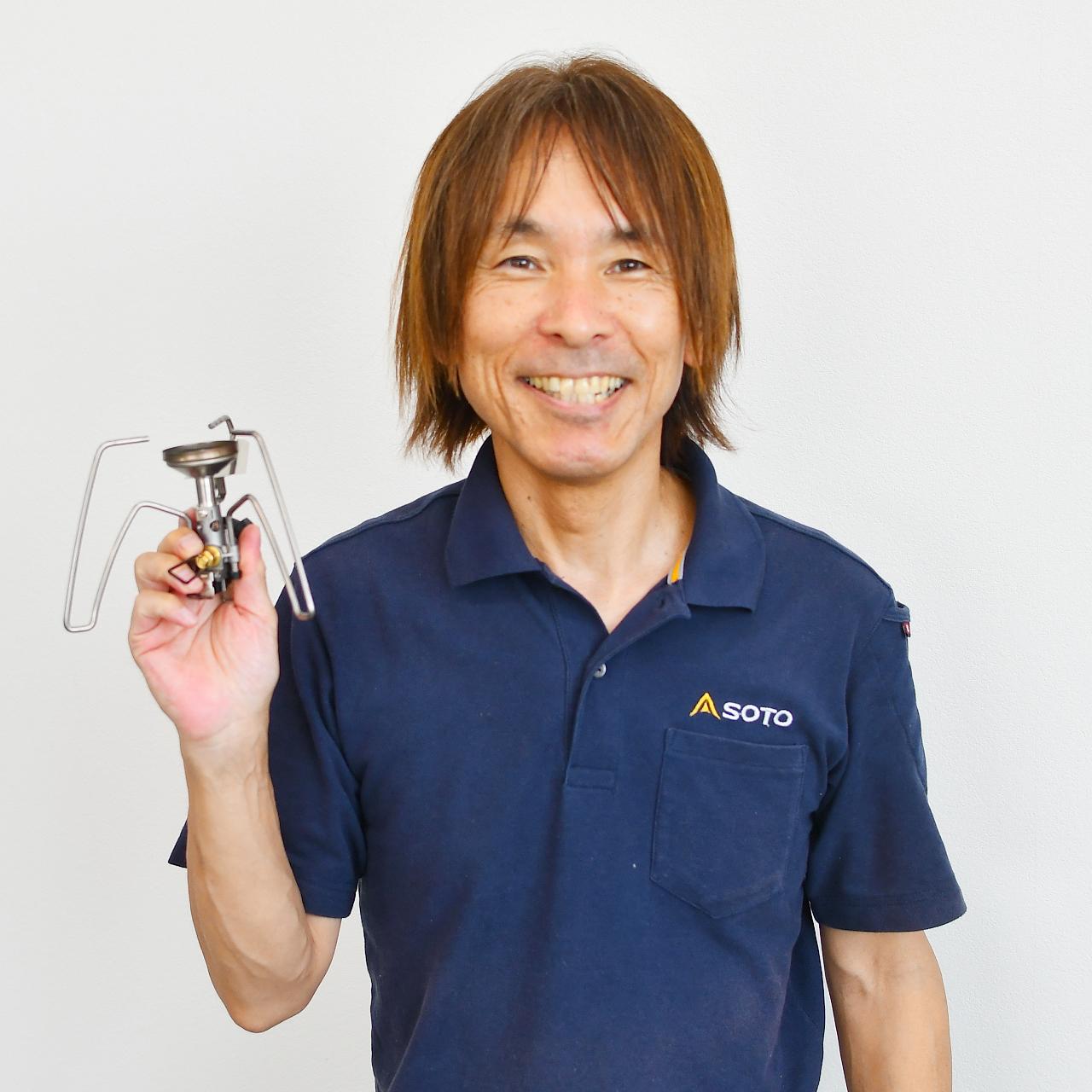
新富士バーナー株式会社
SOTO広報担当
坂之上さん
そうですね、一定の工程ごとに部材を人の目で検査しています。
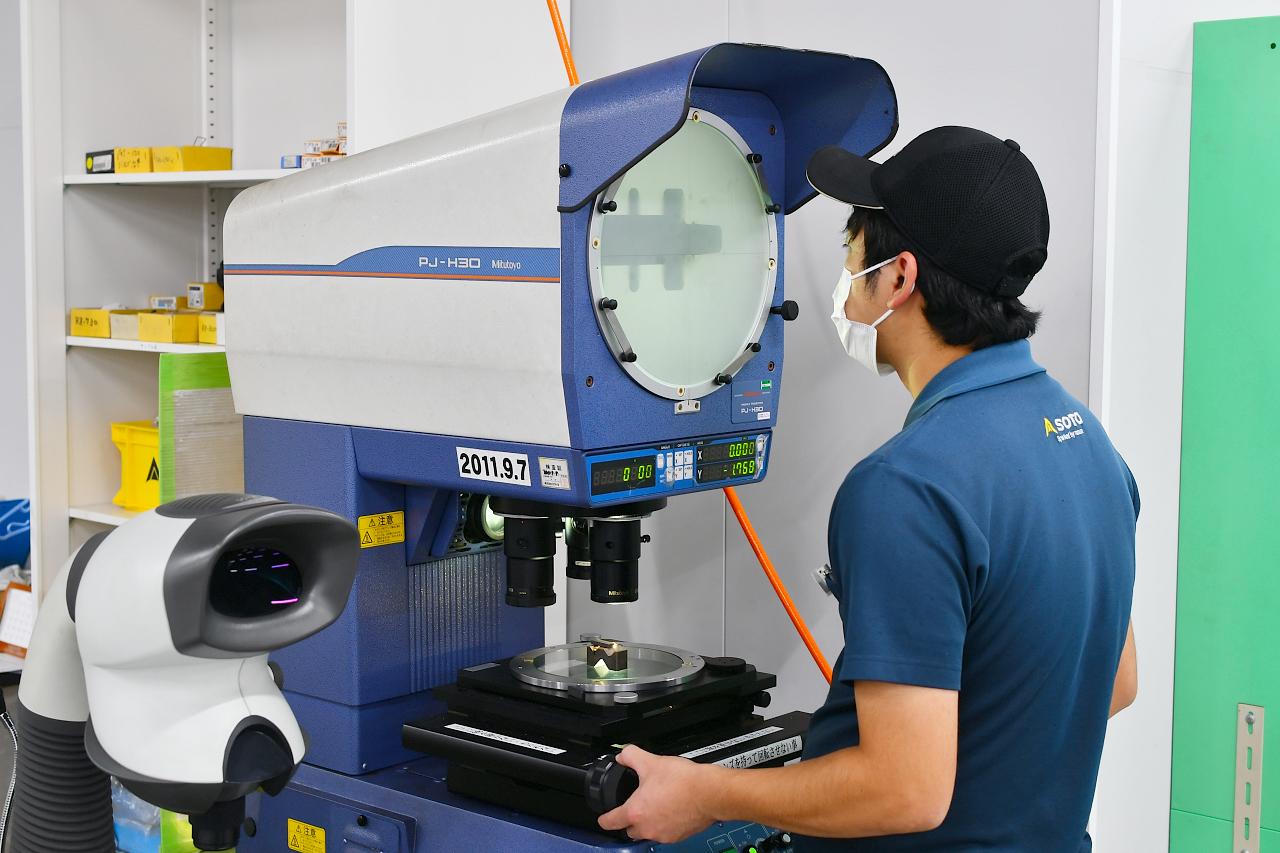
製造業ってみんなこんなに徹底してるんですか?
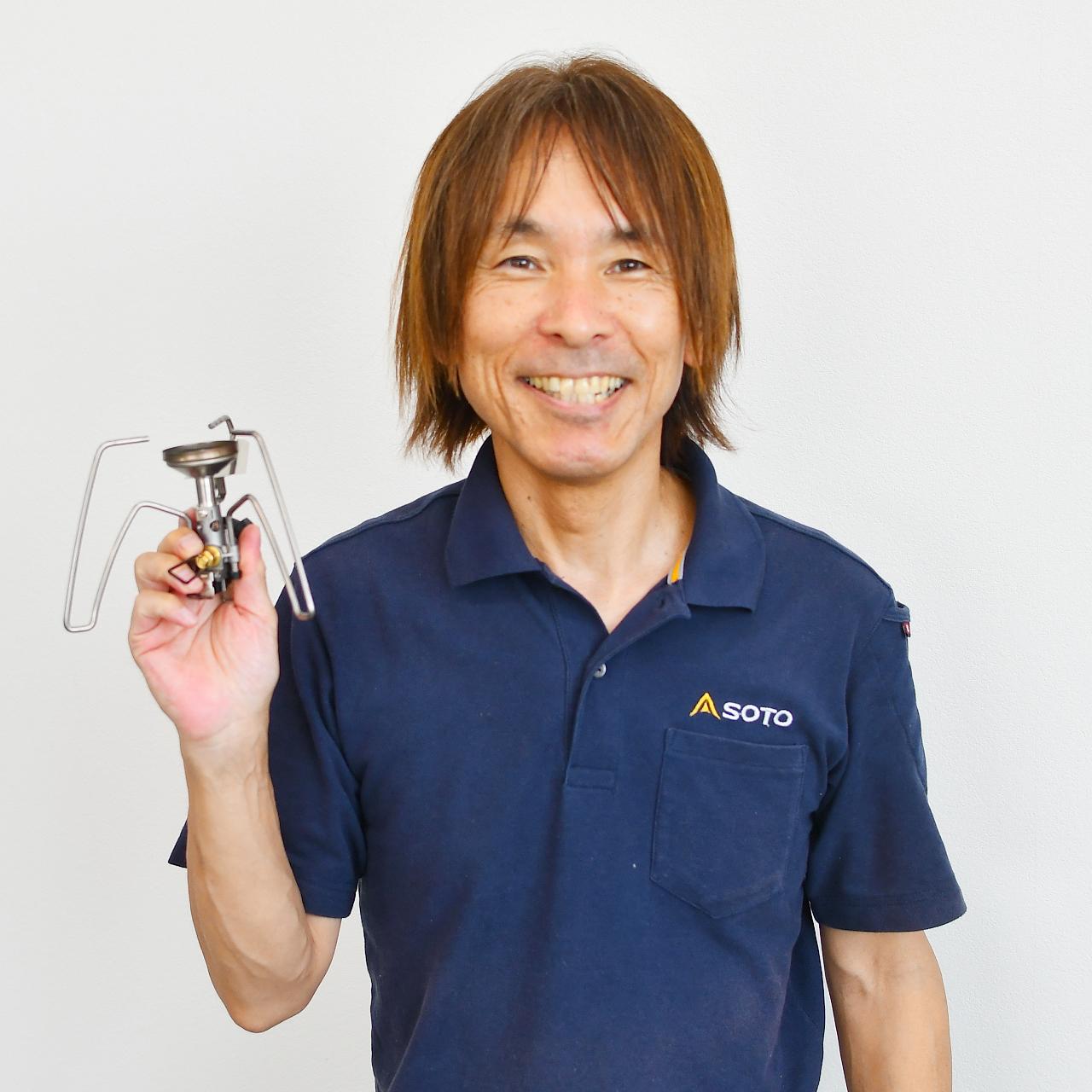
新富士バーナー株式会社
SOTO広報担当
坂之上さん
他社さんの検査方法についてはわからないのですが、もちろんみなさん安全にはこだわっています。
ただ、当社に関しては炎を扱うということで、安全な製品を提供するために、検査の徹底を非常に重視しています。
ですので検査回数や検査方式など、可能な限り高い水準を日々追求しています。
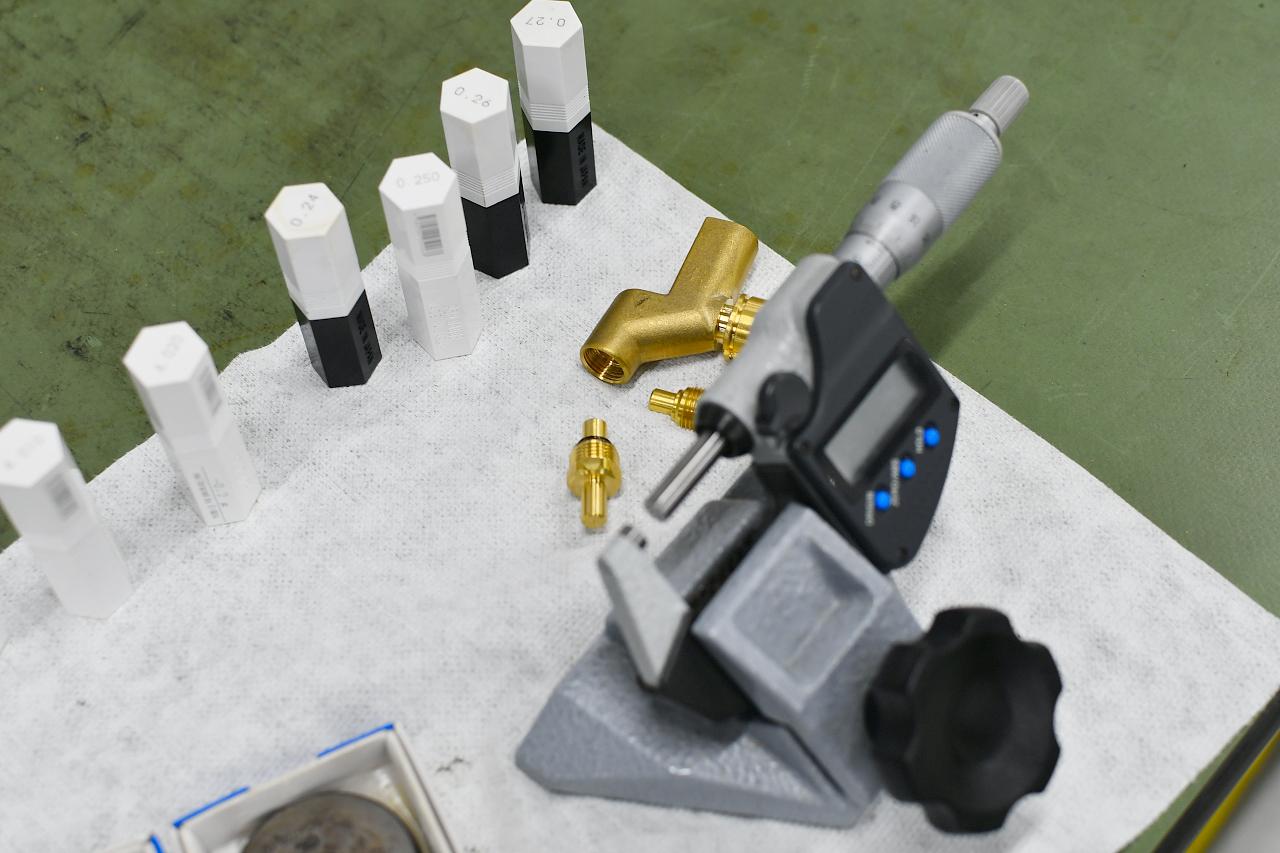
なるほど、感服です。
で、出来上がった部品を洗浄。
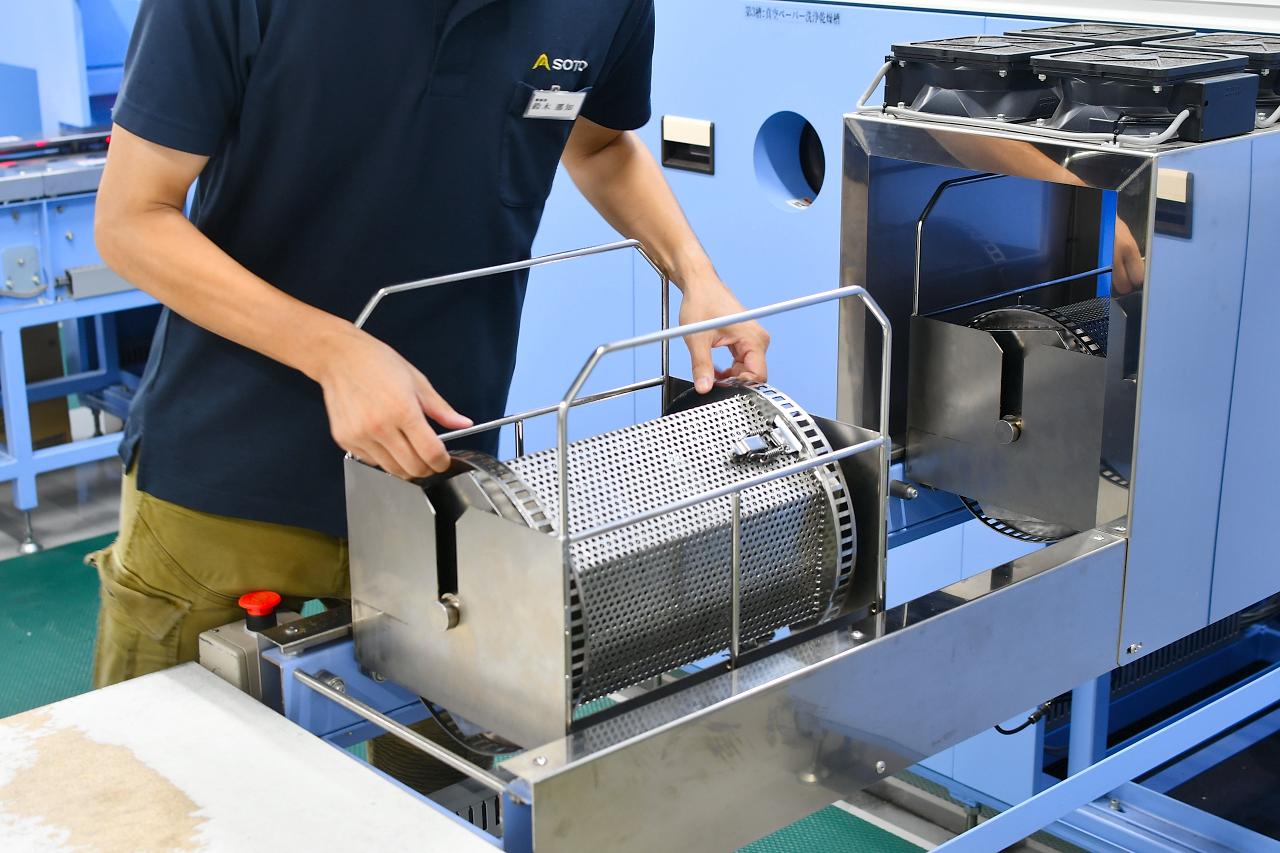
細かすぎて何に使うかよくわからないけど、ピカピカの部品が完成。お次は組み立て工程だよ。
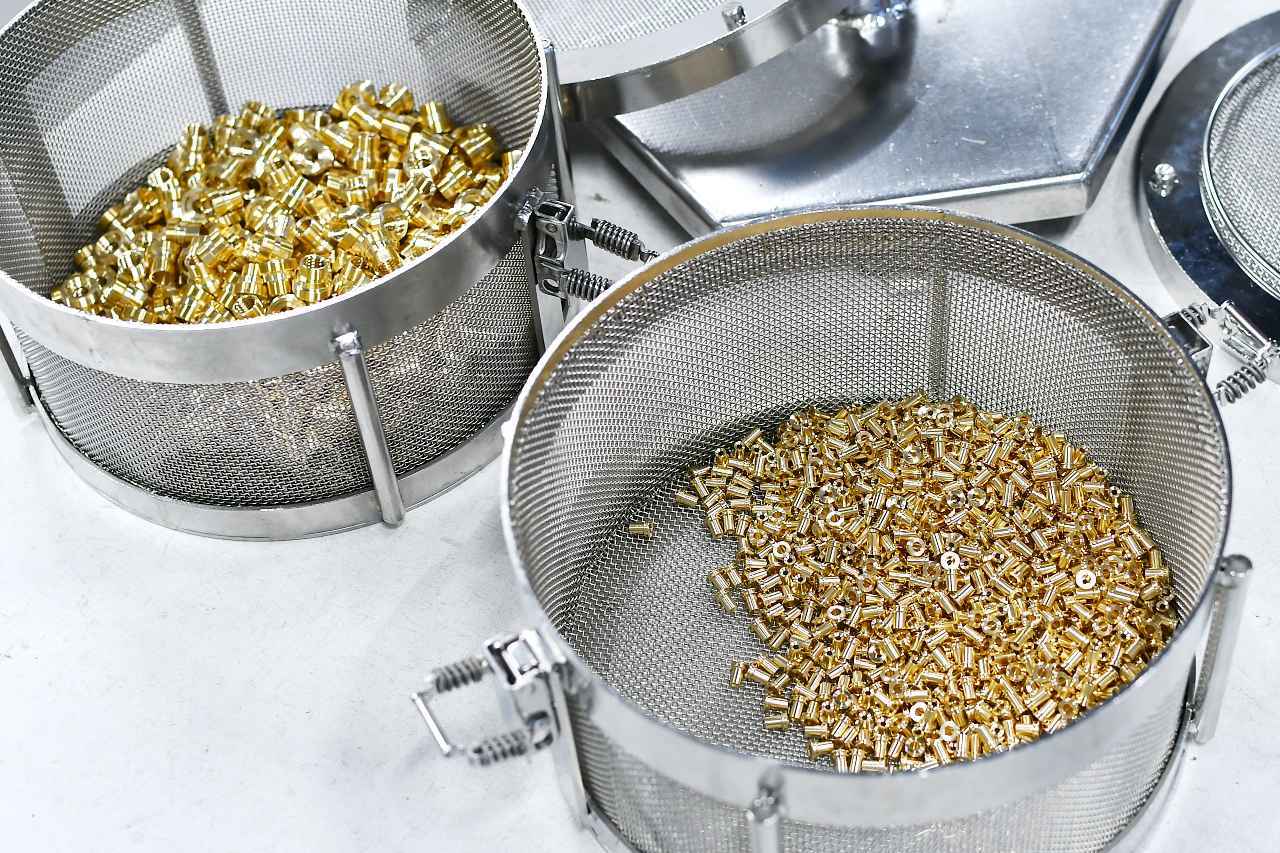
組み立て&検査
出来上がった部品は、2階の組み立て工場でバーナーとして作り上げられるよ。
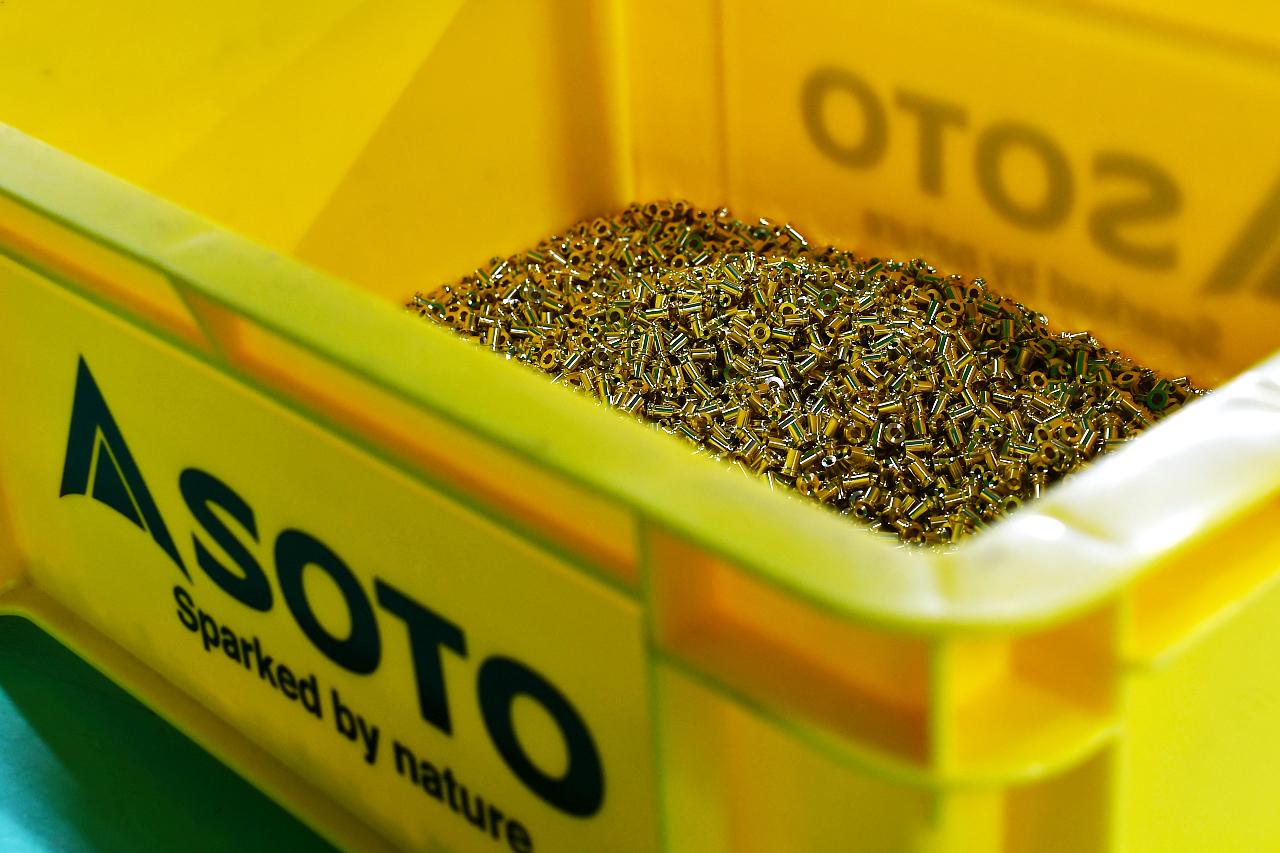
部品が小さいから当然なんだけど、思った以上に精密な組み立て。メインフレーム部分に部品をうちこんでるのかな。
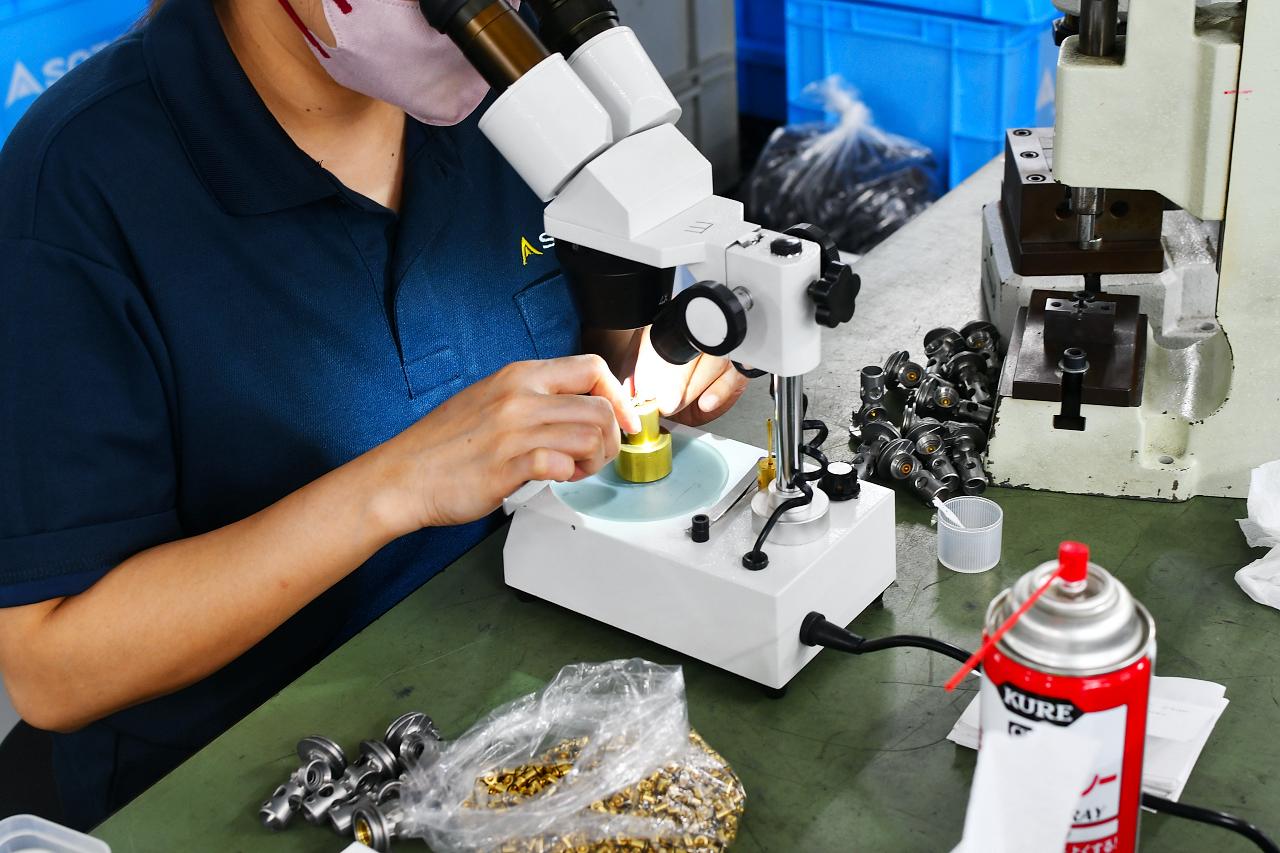
ガス缶接続部の弁とOリングの組み込みかな。あまり見かけない精密トルクレンチ使ってた。
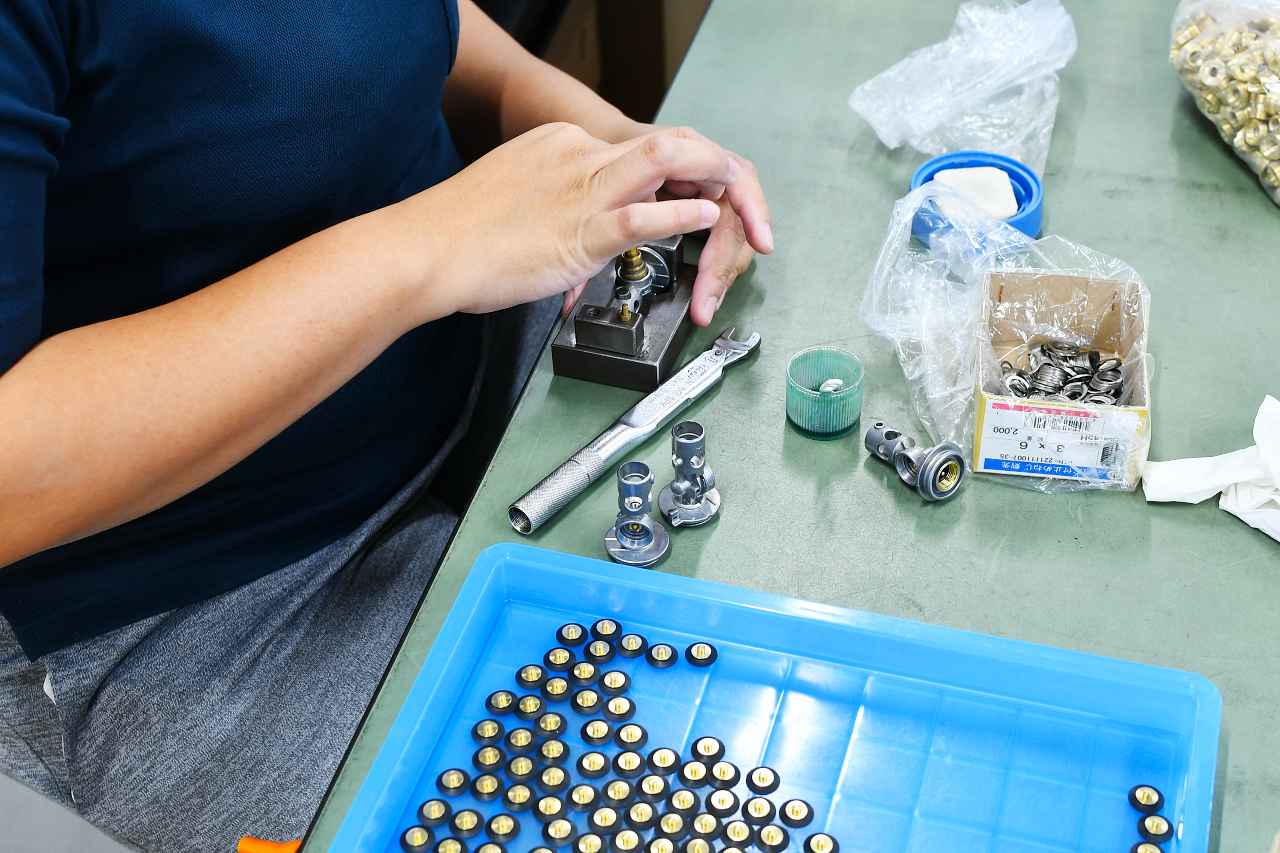
ちなみに、どれくらい細かい作業か伝えるためにカットモデルを見せてもらった。
金属玉がざっくりだけど2mmとかなんじゃないかな。
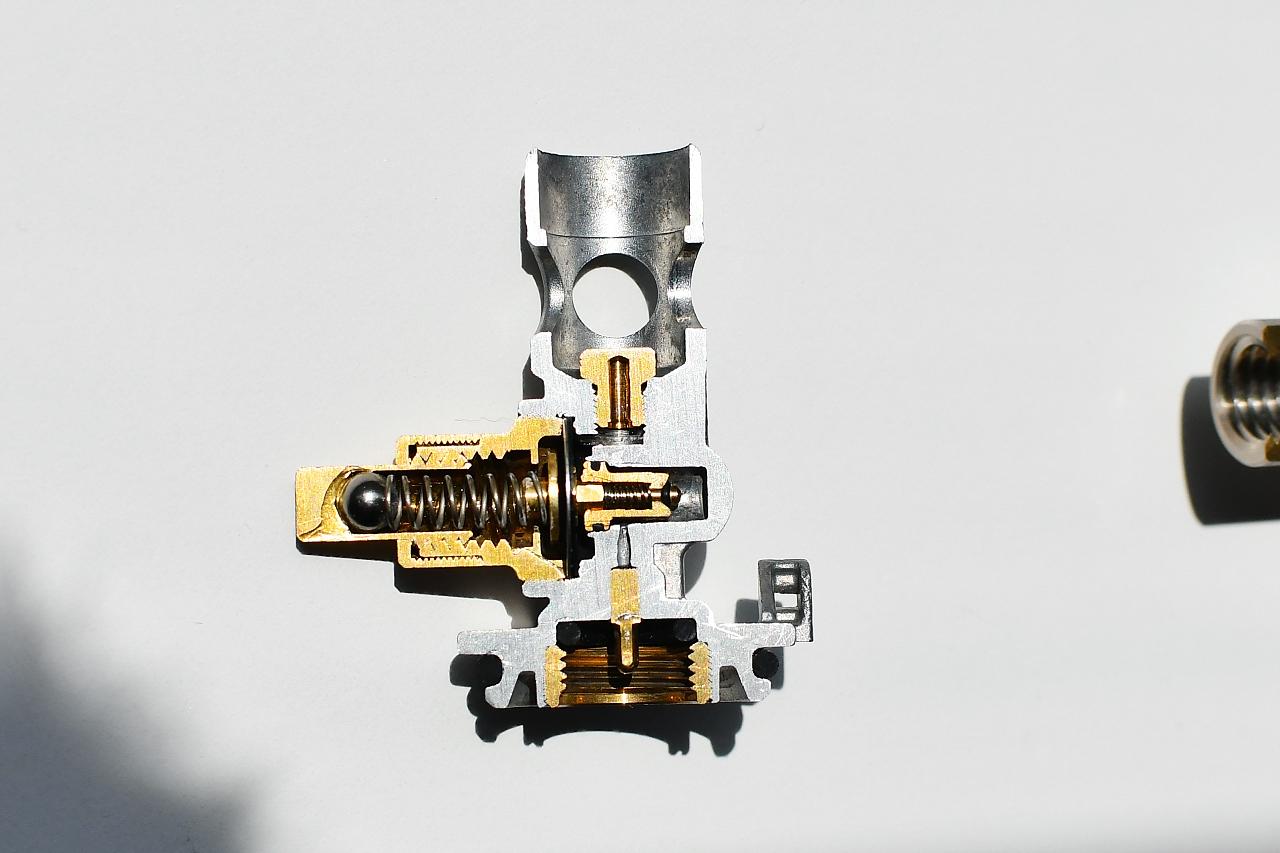
組み立てって、ラインを作って可能限り作業を単純化させてってイメージだったんですけど、一人ひとりが職人さんですね。
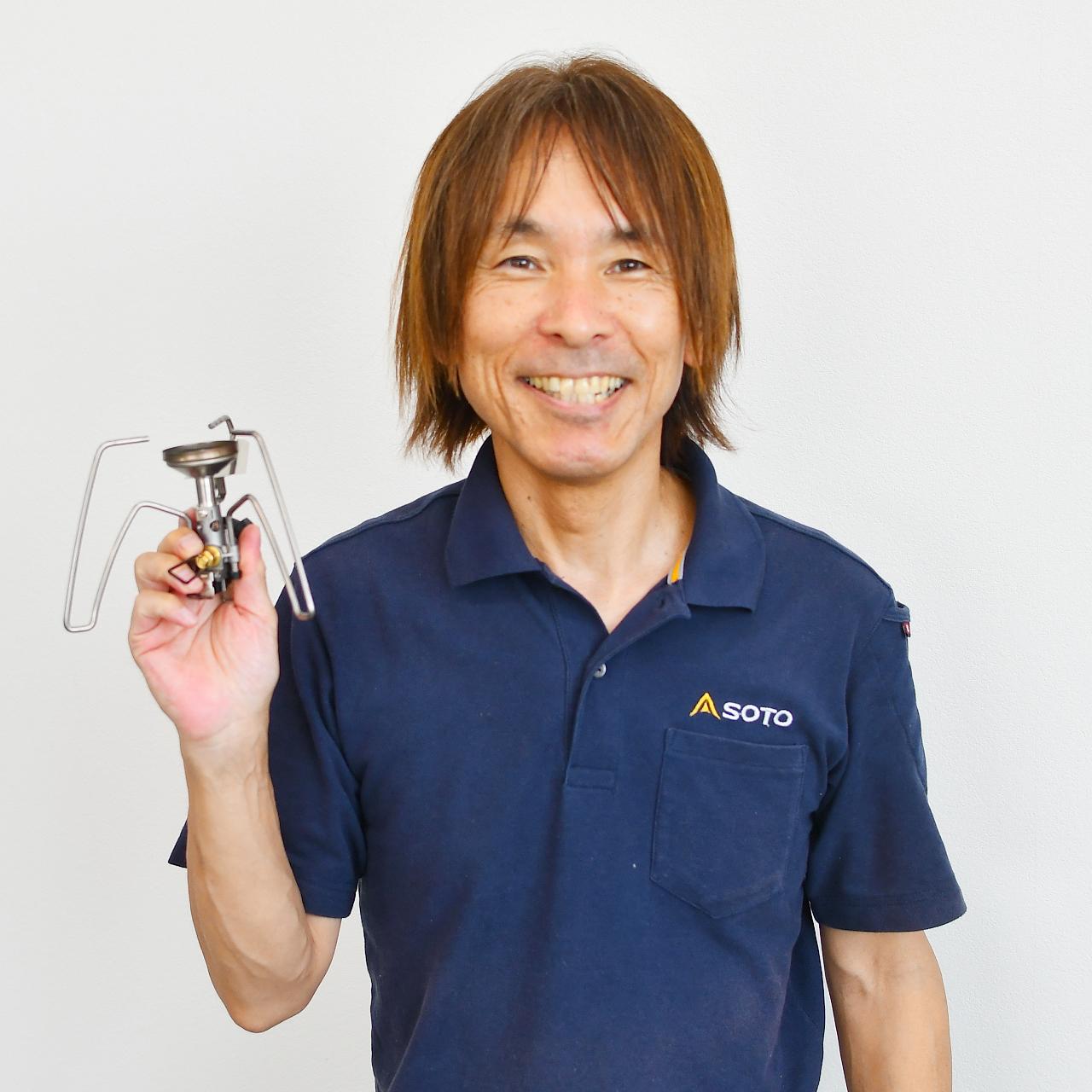
新富士バーナー株式会社
SOTO広報担当
坂之上さん
そうですね、単純作業ではないですね。
実は、当社では基本的にラインを作らないんですよ。
どういうことですか?
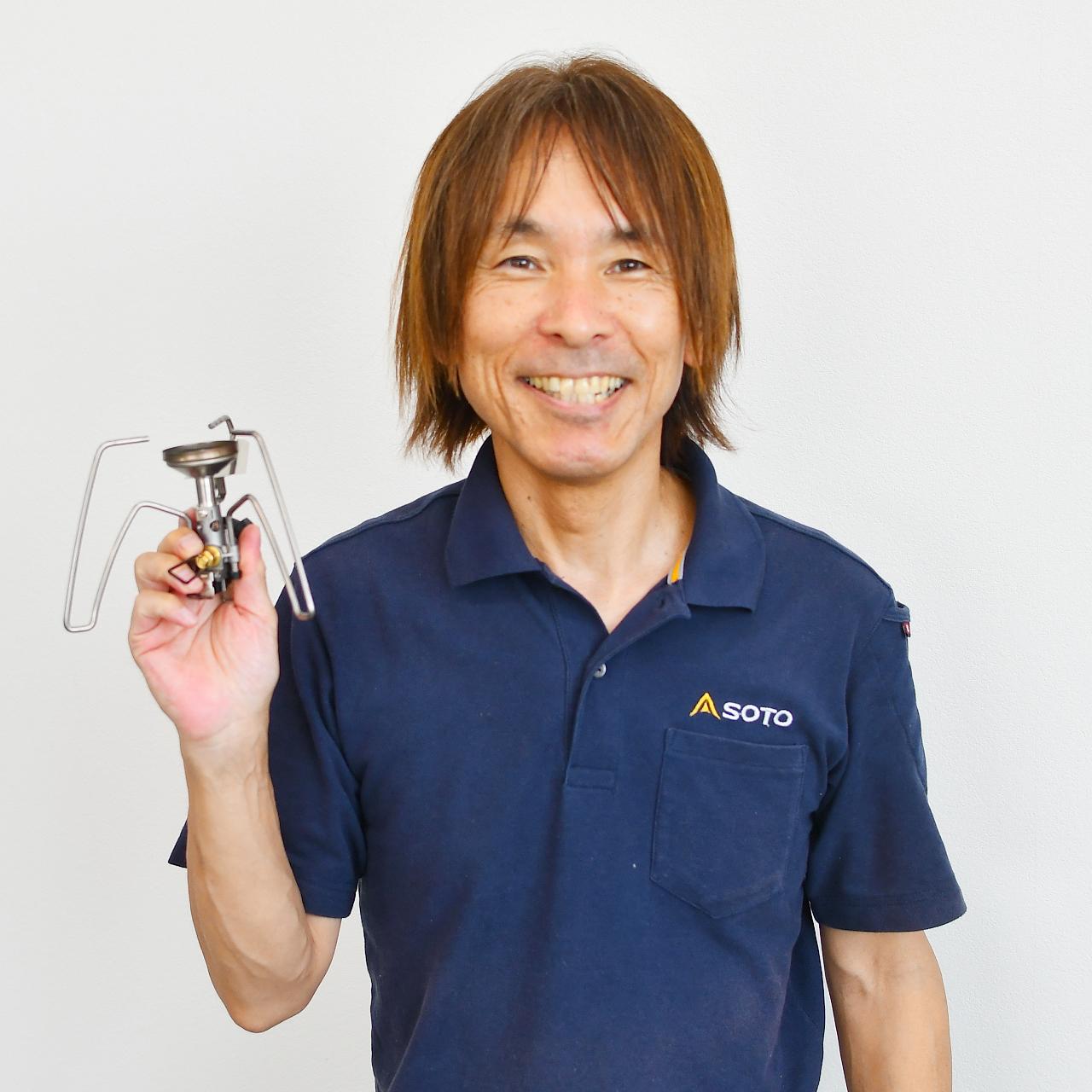
新富士バーナー株式会社
SOTO広報担当
坂之上さん
組み立てチームが複数ありまして、その時の状況に合わせてどのチームが何をどれだけ作るかというのを流動的に対応するようにしています。
なので、チームメンバーはどの作業も担当できるよう、全員がすべての作業に習熟しています。
流動的に対応できるようになってるんですね。言うは易しだけど大変そうな。
あれ、なんか水槽。これはなにやってるんですか?
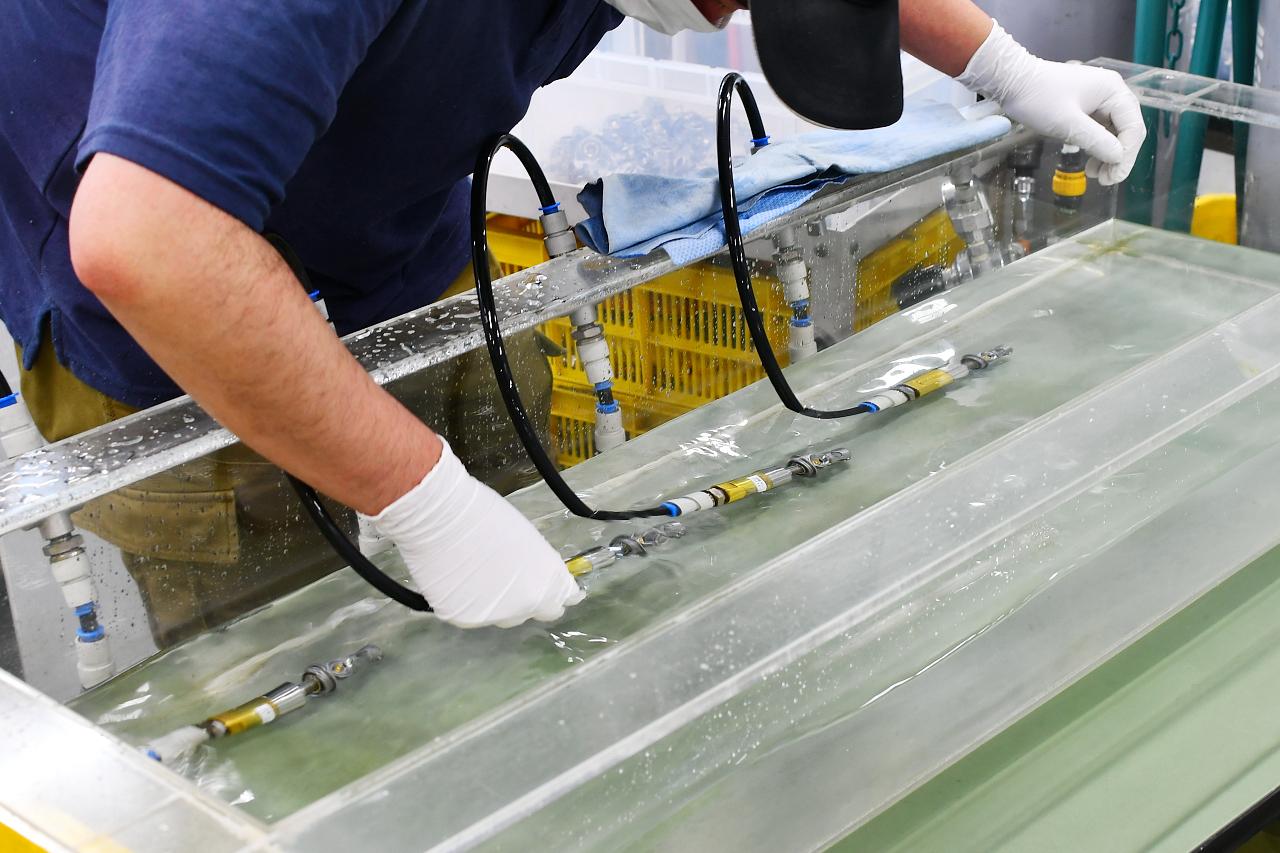
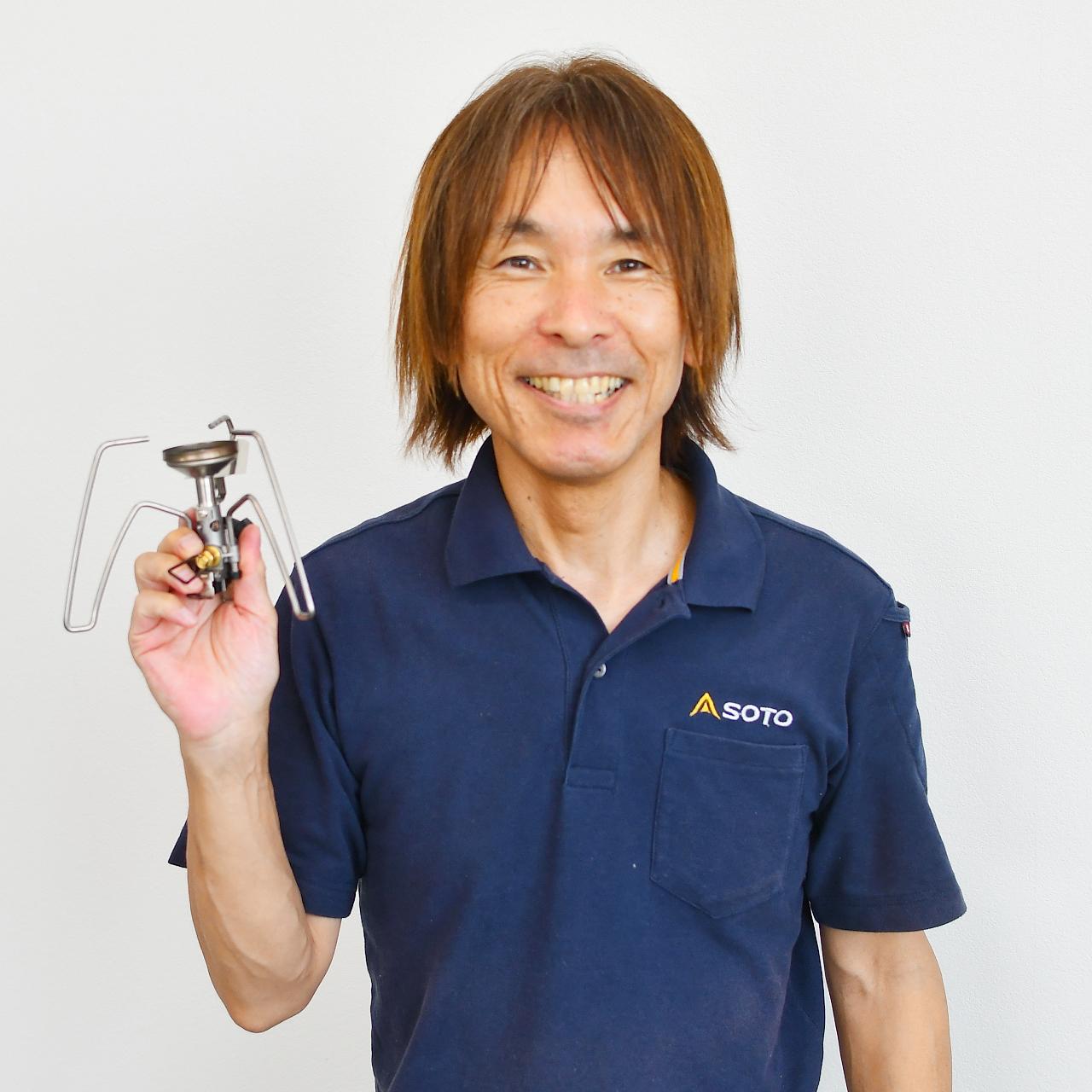
新富士バーナー株式会社
SOTO広報担当
坂之上さん
最初に少しお話しさせていただきました、当社における検査のこだわりがわかりやすい工程ですね。
組み立てた製品を水に沈め、窒素ガスを通すことで漏れを見つけるという検査です。
そういうことですね、窒素ガスをLPガスに見立ててるんですね。
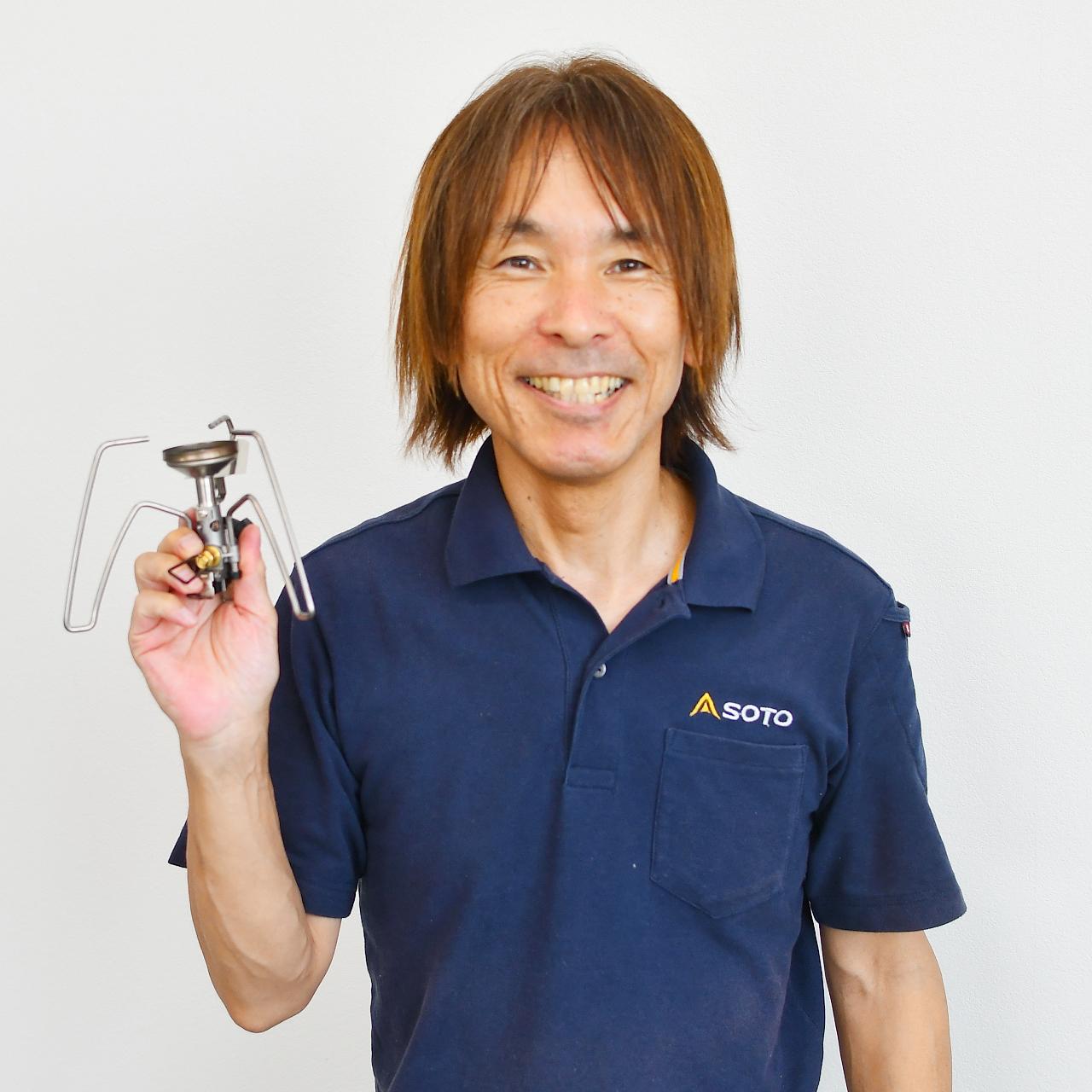
新富士バーナー株式会社
SOTO広報担当
坂之上さん
この方法ですと、万が一漏れが発生した時に、どこから漏れが発生しているのかも特定でき、どの製造工程に、どんな原因があったのか、なども追及できます。
なるほど、シンプルな方法だからこそ、検査として非常に有効なんですね。面白い。
ただ、手間かかりますよね。
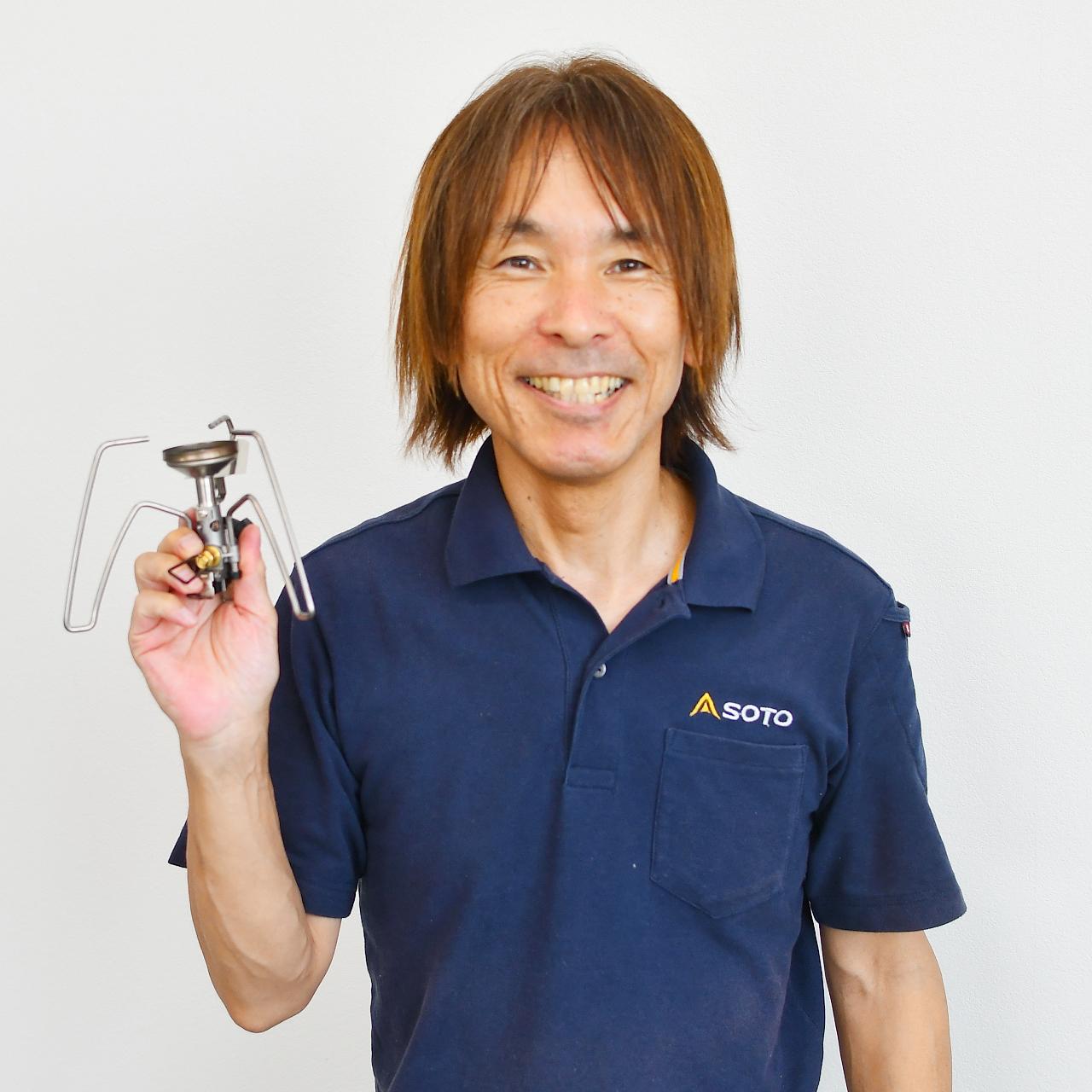
新富士バーナー株式会社
SOTO広報担当
坂之上さん
そこは会社としてのこだわりですね。
なんか四角いブースがあると思ったら点火してた。
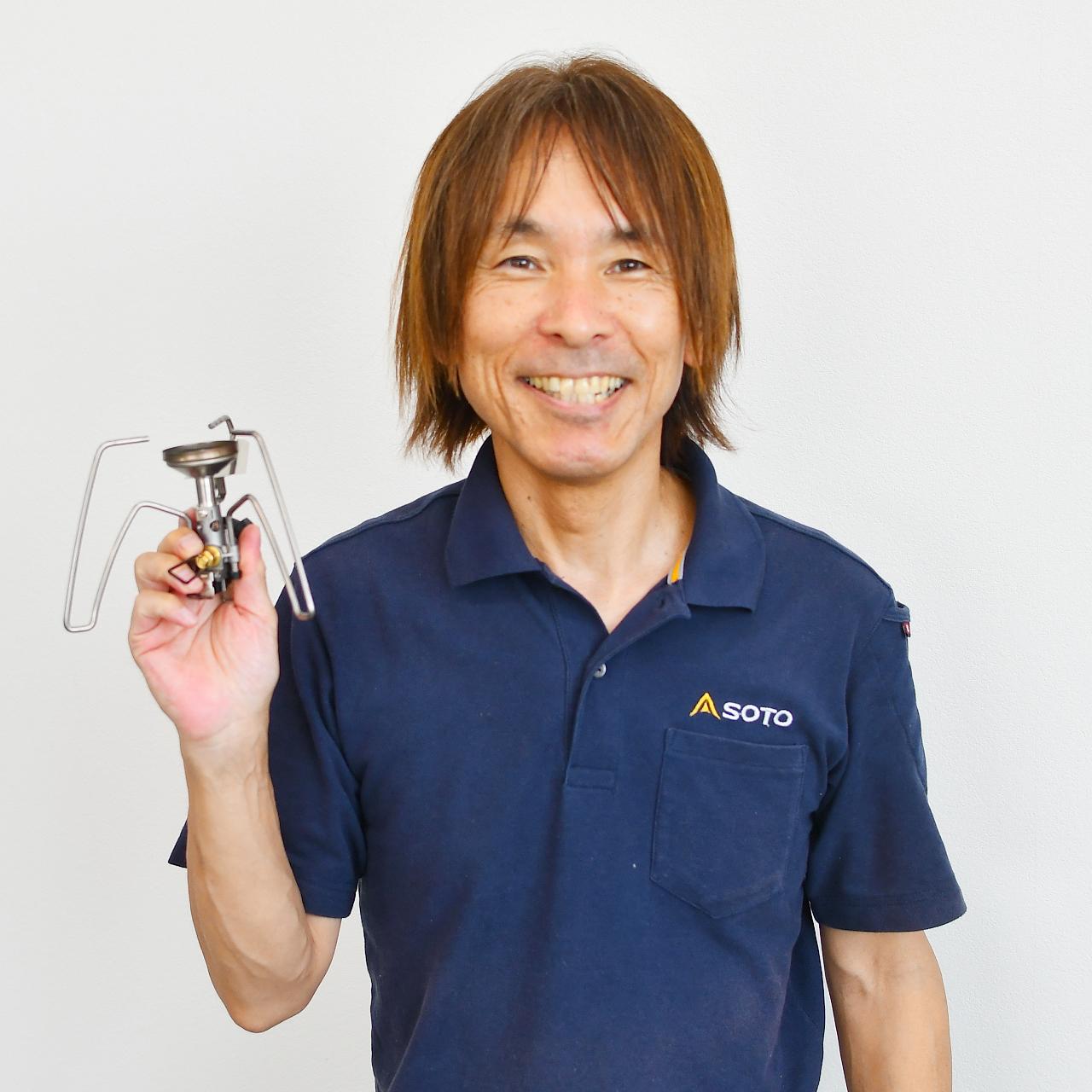
新富士バーナー株式会社
SOTO広報担当
坂之上さん
組みあがった製品は全て実際に発火テストを行っています。
あ、じゃあ自分がモノタロウで買ったST-320とかも、出荷前に一度は火が入ってるんですね。
というか、ここまでにもめっちゃ検査しまくってますよね。
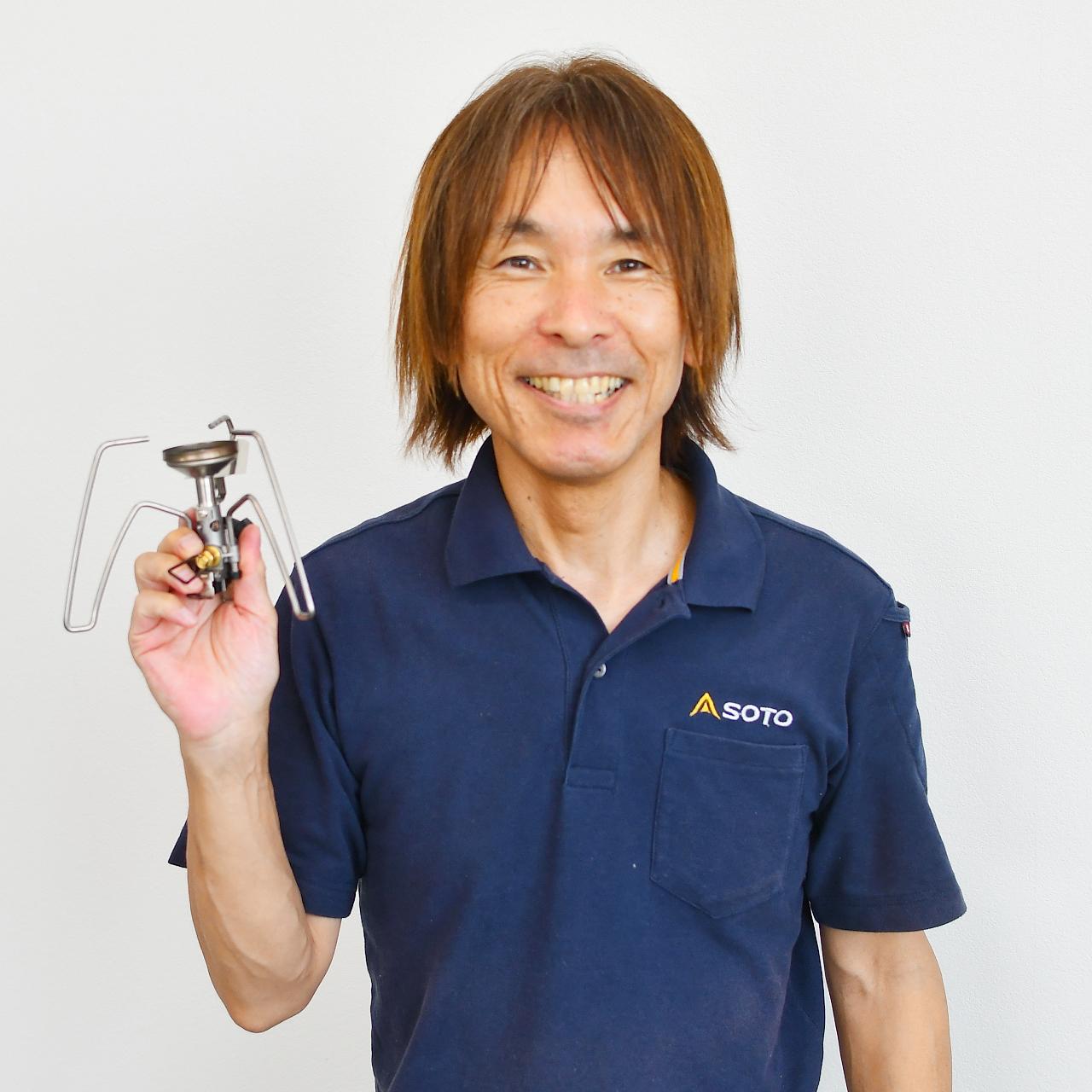
新富士バーナー株式会社
SOTO広報担当
坂之上さん
そうです、世にあるすべてのSOTO製品は、こうした検査をすべてクリアしています。
発火テストに至るまでに各種検査をクリアしていますが、やはり最後はLPガスを使って実際に燃焼させて検査することで、ガス漏れがないか、点火性能は良好か、炎は正常か、などをチェックしています。
新品を購入したのに火口に焼き色がついていたとしても、それは徹底した検査の証ととらえていただければと思います。
なるほど、炎の漏れを見るために黒いブースなんですね。
いやなんというか想像以上のこだわりっぷりで興奮しますね。
まとめ
こうして世に出るSOTOのバーナー。内部がこんなに精密だとは正直思ってもみなかった。
バーナー専業メーカーとしてのこだわりがほんと凄い。
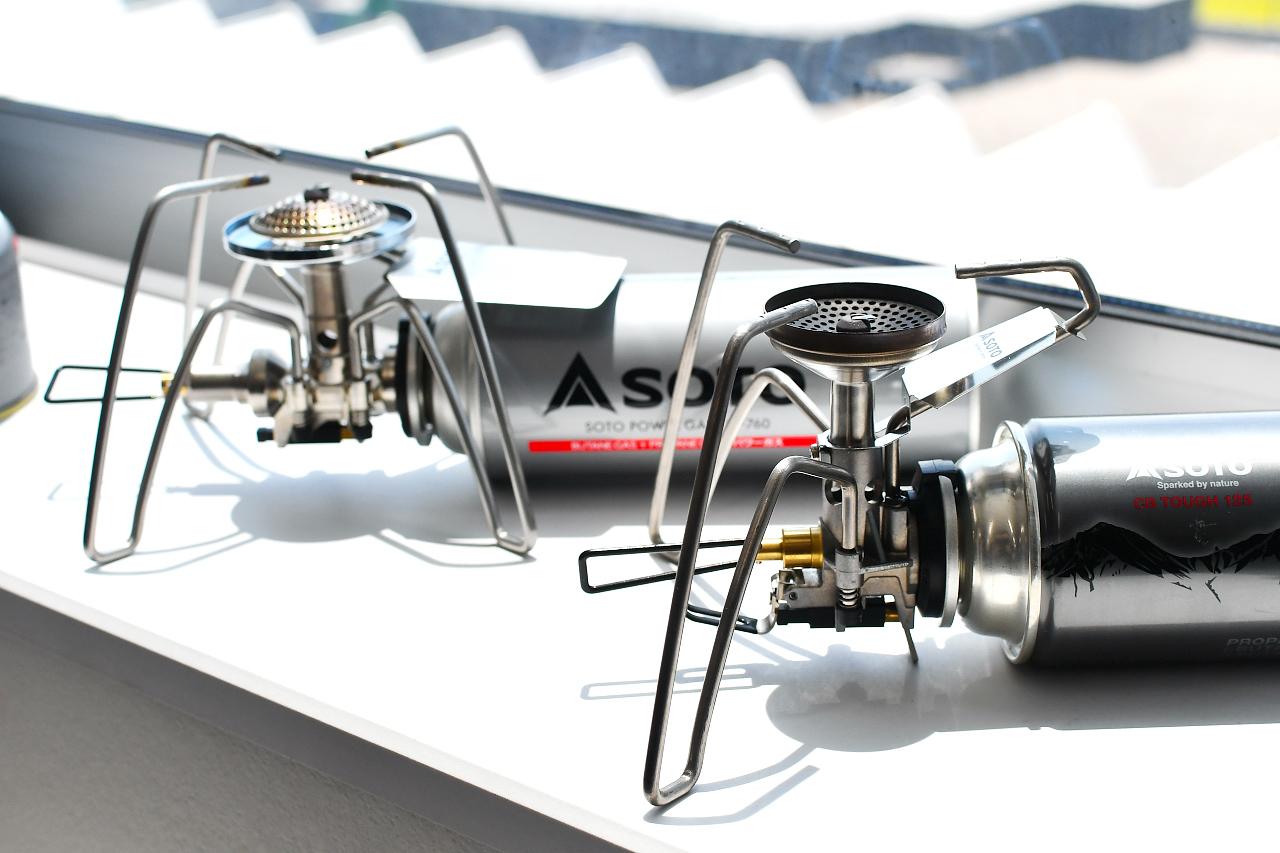
あとマイクロレギュレーターの機構にしびれたので、取材終わって帰宅するなりamazonでST-350をポチった。ST-350の初期ロットはST-350TBっていって、CB TOUGH 125が付属するお得セットなのよ。
これね。
ソト(SOTO) 日本製 シングルバーナー マイクロレギュレーター搭載(高火力 風に強い) CB缶 軽量 コンパクト 収納ポーチ付 ハイパワー カセットボンベ ソロ デュオ キャンプ トレッキング 登山 レギュレーターストーブ TriTrail(トライトレイル)・CB TOUGH 125セット ST-350TB
amzn.to今回は製造工程のこだわりを教えてもらったけど、ほかにも面白い話をたくさん教えてもらったので、まだまだSOTOの記事は続くよ。
取材協力:新富士バーナー株式会社、レポート:若林浩志